Technology development in Statoil

Development and effective application of innovative technology will be highly significant in every industry for improving competitiveness and meeting changed customer needs and demands. But introducing new solutions, or different applications for existing methods, always involves a degree of risk. As a result, the path from idea to successful application usually goes via a detailed review and analysis of the business concept, small-scale testing – with possible laboratory trials – to a full-scale test where possible. How has that been manifested in Statoil/Equinor’s adoption of technological advances?
Favourable preconditions
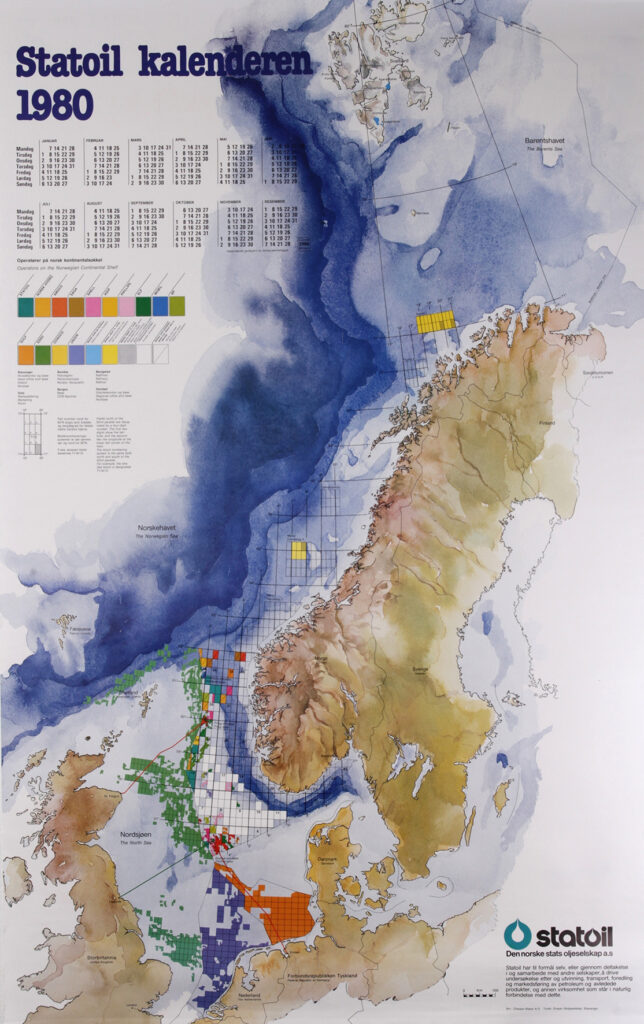
Statoil and the Norwegian Petroleum Directorate were both founded in 1972. A goal right from the start was that the former should become an integrated oil company with operations throughout the value chain from exploration, via development and production, to product sales.
The timing of Statoil’s start-up was favourable. Technologies which made it possible to drill wells and produce oil from facilities in waters up to about 100 metres deep were relatively new. They had been developed in the USA since the late 1940s, and were imported to Norway with the first exploration drilling on the Norwegian continental shelf (NCS) in 1966. That made it possible to explore for petroleum in the relatively “shallow” southern end of Norway’s North Sea sector, where the giant Ekofisk discovery and the Frigg gas field were proven in 1969 and 1971 respectively.
Norway had farsighted politicians who set clear goals for the new industry, including requirements on Norwegian content, participation and control. Professional parameters and guidelines to govern the sector were established by civil servants. The “Norwegian model” was developed, with a clear division of roles and responsibilities between the Storting (parliament) and the relevant ministry, the NPD as the regulator, and Statoil and others as the oil companies.
The country’s supplier industry could benefit from its expertise in the maritime sector – such as the development of Aker’s H-3 drilling rig – in shipbuilding – like Kværner’s gas carriers – and in large construction projects – including concrete dams and bridges. A tanker shipping crisis from the 1970s prompted shipyards to convert to offshore fabrication. Oil prices also rose sharply during this decade because of growing global demand as well as political unrest in the Middle East. That allowed Statoil to develop into a company which came up with solutions to the special challenges presented by the NCS, with deep water and tough weather conditions.
Statpipe and concrete platforms – first steps on the technology ladder
One of Statoil’s most important fields has been Statfjord, which was proven during 1974 in the Tampen area of the North Sea. Water depths on the field vary between 120 and 250 metres. Planning a landfall for its associated gas was the first development study Statoil undertook on its own account.
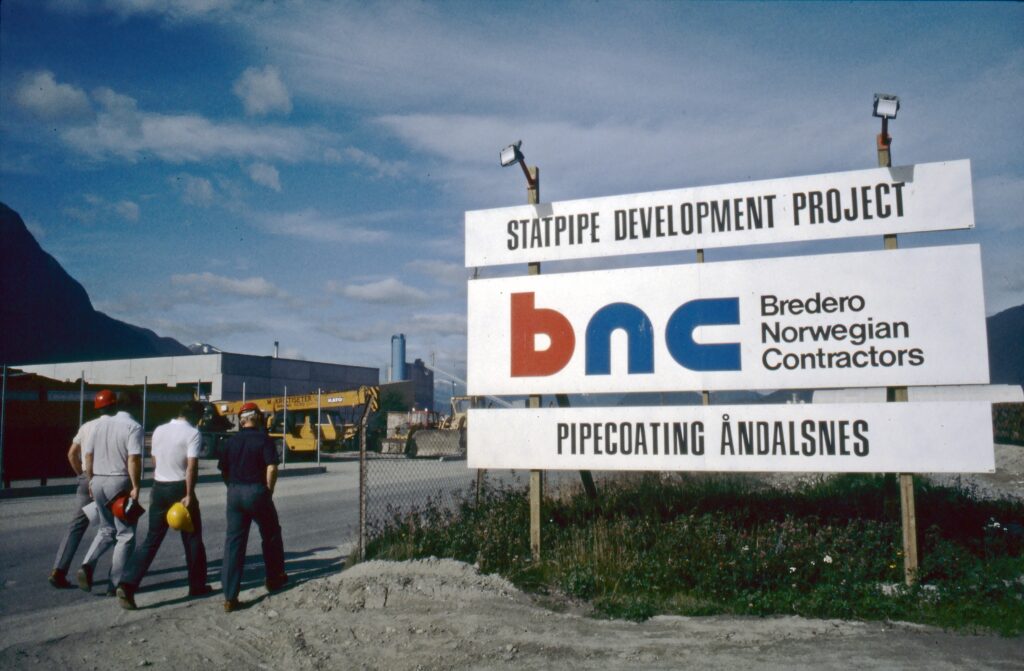
The authorities required that oil and gas should be landed in Norway, if feasible, to ensure maximum national value creation. But the Norwegian Trench, an underwater valley with water depths down to 300-400 metres, lies between the Tampen area and the west Norwegian coast. This challenging obstacle presented a number of unresolved technological problems. The study project, which began in 1976, became an important forerunner to the construction of the Statpipe pipeline and its Kårstø terminal north of Stavanger – and for the leading position Statoil eventually acquired in the installation and operation of offshore pipelines.
On the platform side, personnel from the company were seconded to and incorporated in Statfjord operator Mobil’s project organisation. The US company’s development concept was three platforms with integrated topsides for production, drilling and quarters (PDQ), supported on concrete gravity base structures (GBSs). Such installations offered a number of advantages:
- they were suited to the water depths on Tampen
- they had a long commercial life and could support a topsides weighing 50-60 000 tonnes
- most of the work could be completed at shore
- large oil storage could be incorporated in the structure
- Norwegian industry had good expertise with concrete
- they could be built locally in Norway.
Planning and executing the Statfjord development with Mobil put Statoil through a very important learning phase. That included developing new and efficient buoy-loading systems for offshore use.
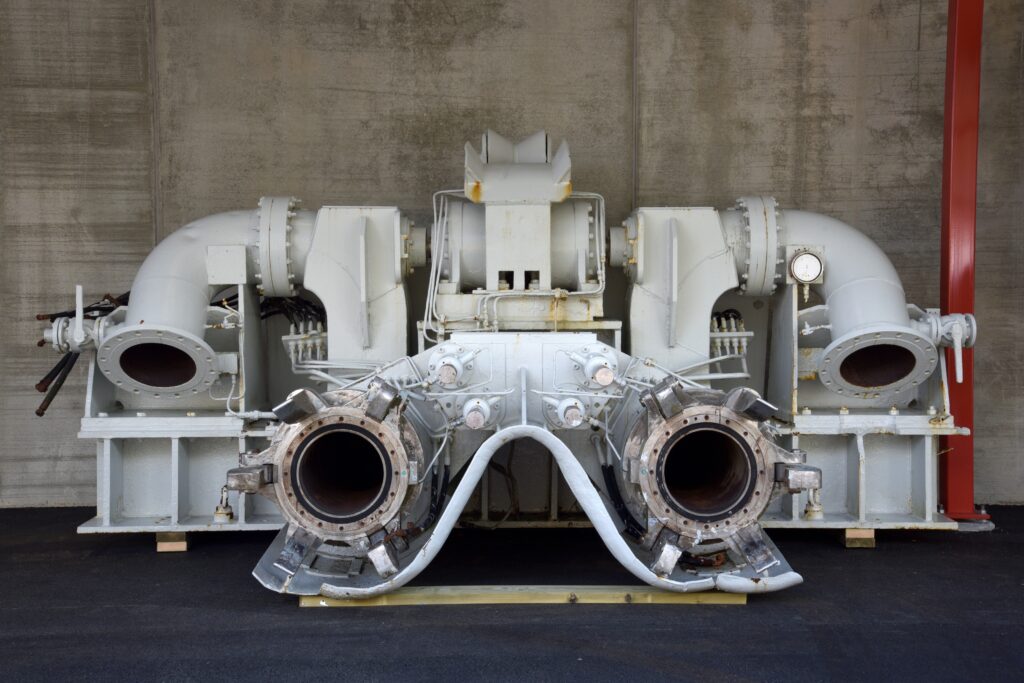
The company eventually became the leading specialist on the NCS for pipeline transport of gas and oil. In its time, Statpipe ranked as the world’s longest underwater pipeline. The challenges posed by the Trench were overcome, with technologies developed to carry out repairs in waters down to 360 metres. Divers worked in a nitrogen-filled habitat which protected them from direct exposure to seawater. More effective methods for trenching and protecting seabed pipelines were devised.
Since it was clear that pipeline repair methods would be needed in even deeper waters on the NCS, a major development project was launched to come up with solutions for completely diverless welding and repair.
Another area where Statoil made a big contribution was research on maritime materials technology. Treating and transporting corrosive wellstream in a tough offshore environment presented many challenges and surprises. Statoil established labs in Stavanger and later in Trondheim which became highly significant for the choice of materials in new equipment and solutions.
Gullfaks in Norwegian
Statoil’s first operator role was on the Gullfaks field, which also lies in the Tampen area. The licence covering this reservoir was awarded in June 1978, with the first discovery made a month later. Planning for the initial production phase began in early 1980, with a plan for development and operation (PDO) submitted to the government late that year and approved by the Storting in June 1981. Gullfaks became the company’s first full-scale lab for developing a number of technologies.
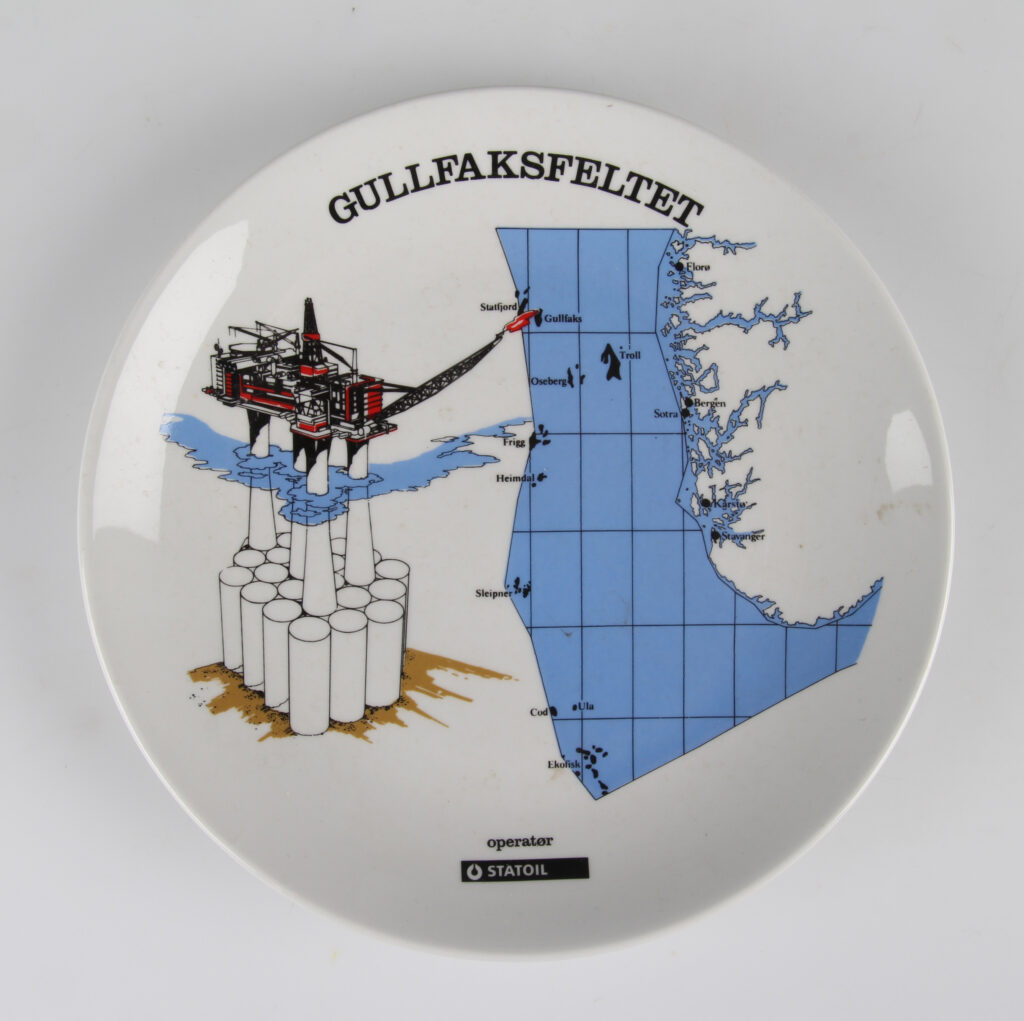
The initial development phase covered two large platforms, Gullfaks A and B, with associated loading buoys. This was the first field to be developed with only Norwegian licensees, a Norwegian operator, Norwegian as the working language and largely Norwegian suppliers. No less than 80 per cent of the contracts for the A and B platforms were awarded to domestic companies. Gullfaks A was incorporated in a very close collaboration with industry in Norway, where the Federation of Norwegian Engineering Industries (MVL) was by far the most important partner.
A great deal of groundbreaking work was done by the project in many areas to improve technical solutions. A new T-shaped design for the concrete platform and its topsides was developed, for example. Since wells drilled from the Gullfaks platforms would be unable to reach the whole reservoir, a number of subsea wells were also planned. The idea of drilling these before the platform was completed meant that the field came on stream earlier than originally planned, with the first subsea well starting to produce on 22 December 1986. Another couple of such wells were in swing before the first platform well was ready in the spring of 1987. The contract for producing the five subsea wells and a reserve for tie-back to Gullfaks A was awarded to the Kongsberg group.
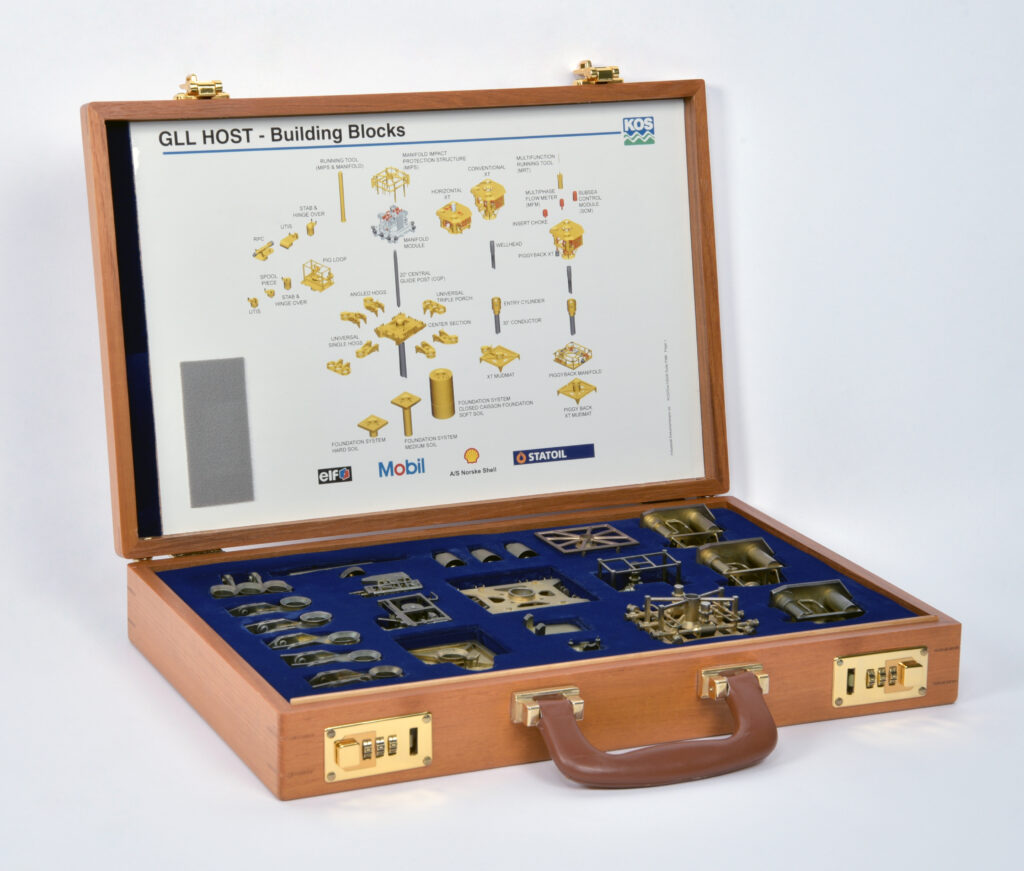
Collaboration between this company and Statoil had begun as early as the 1970s, when Kongsberg had an agreement with America’s Cameron Iron Works on producing wellheads and other essential equipment. Experience gained by Kongsberg from earlier studies of Statoil’s future Tommeliten development could be applied to Gullfaks. So could the results of research and development projects conducted by France’s Elf and Anglo-Dutch Shell to try out subsea technology solutions.
The most important innovation on Gullfaks emerged because Statoil had decided that solutions should be developed for subsea wells which could be installed and operated without diver support. This decision was taken following a number of serious diving accidents. If unavoidable, it was possible to dive reasonably safely to about 200 metres. However, the Norwegian Underwater Institute (NUI) in Bergen staged simulated descents to 400-500 metres with a view to an emergency response for damaged pipelines crossing the Trench. Statoil contributed financially to this research.
Since the Gullfaks C platform was to be placed in 215-220 metres of water as part of the second development phase, devising and testing diverless systems was desirable. This would initially be done in 140 metres, where it was still possible to send in divers if anything were to go wrong. So yet another groundbreaking job was done on Gullfaks A by installing the first subsea wells which needed no form of diver assistance. This has since become the norm for most underwater installations on the NCS.
In connection with the further development of concrete platforms, Statoil became extremely competent in geotechnics and foundation engineering. Both Gullfaks C and the Troll A platform have deep “skirts” – the concrete rim which surrounds the tanks at the base of the GBS. Those on Troll A are about 35 metres tall. Bucket foundations/suction anchors have subsequently been developed on the basis of this expertise, and are used both for steel platforms and with many subsea structures.
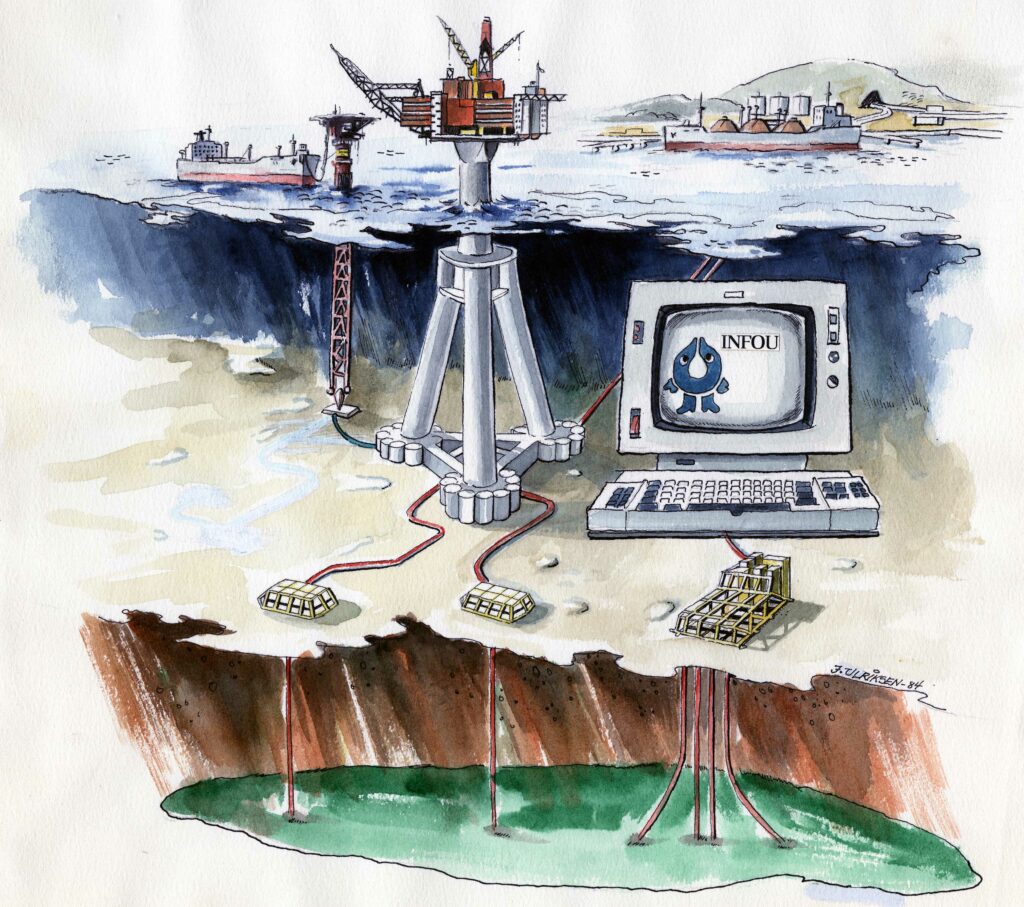
When oil prices slumped in the mid-1980s, a completely new concept was introduced and adopted on the Veslefrikk field. A steel jacket was installed to support the drilling structure, with a semi-submersible process platform tied to it by a bridge. This ranked as the first floating production facility on the NCS. Experience from Veslefrikk became important for later floating platforms, and not least for the further development of flexible hoses.
Other examples of innovations related to Gullfaks are that it was the first field with freefall lifeboats. Another was the introduction of single cabins. The field later became the first to eliminate permanently lit flares through the use of an ignition technology developed in-house.
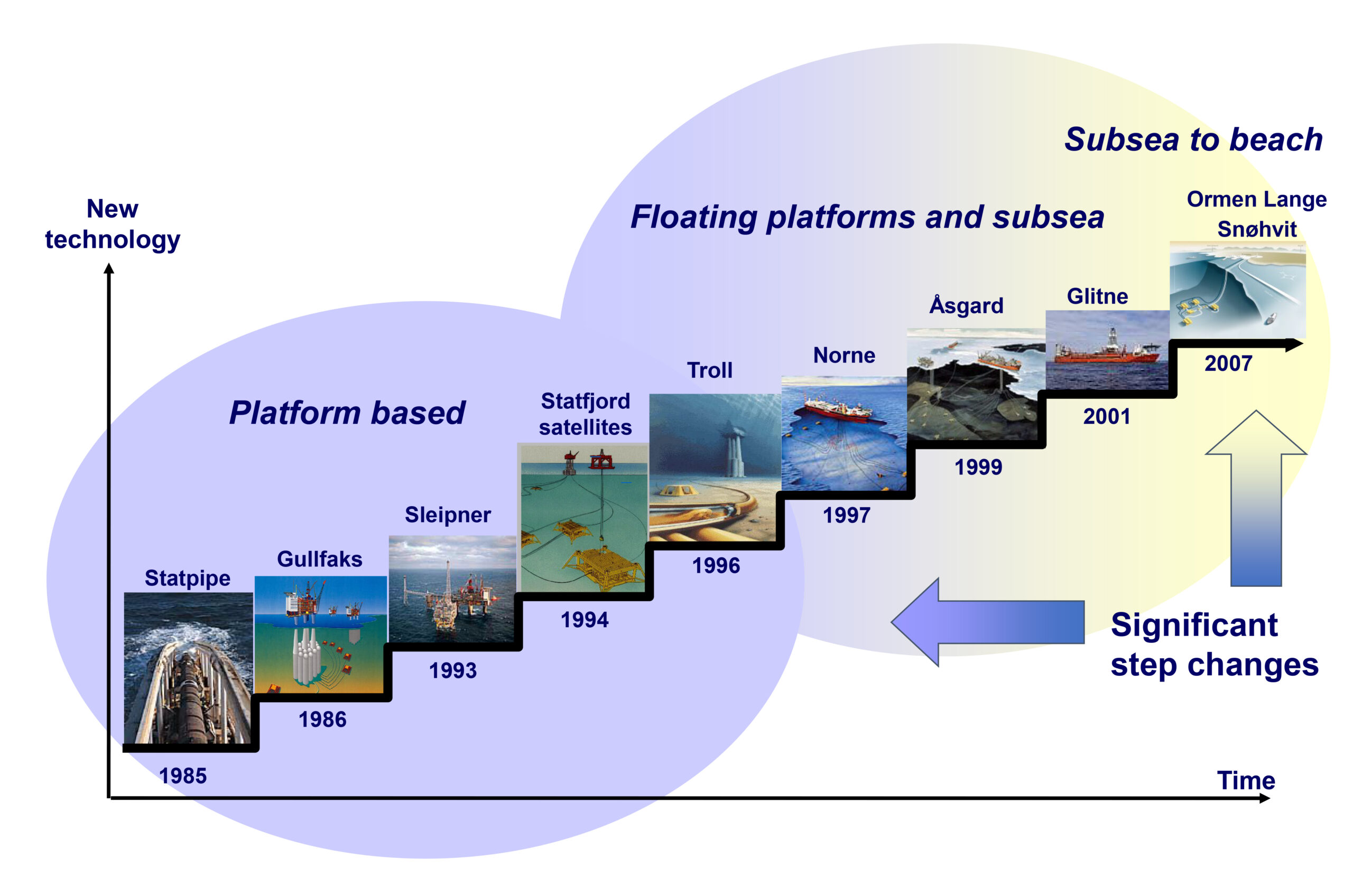
Subsea solutions
Implementing new solutions in development projects requires that all components in the technology have already been developed and tested. In the late 1970s, attention was concentrated on devising solutions which allowed the oil companies to develop fields without the need for surface installations.
Where Statoil’s work on such subsea solutions is concerned, the groundwork was done on Tommeliten and Gullfaks in the 1980s. Its third underwater project was the Statfjord satellites, where the company joined forces with Kongsberg Offshore on the systematic development and standardisation of subsea technology. These standards were further developed through the Norsok initiative in the 1990s, are used globally today and form an important foundation for Norwegian underwater deliveries.
Thanks in part to these initiatives, Statoil became one of the leading oil companies in developing and operating fields with a large number of seabed wells. That was manifested on Åsgard in the Norwegian Sea (see below).
For production to function from subsea wells tied back for a fixed or floating platform, or directly to land, it must be possible to transport the wellstream over some distance without problems. Research was needed to find good solutions here.
During the 1980s, Statoil was very active in work on multiphase flow – the movement of oil, gas and water mixtures through a pipeline. Research on and testing of solutions were conducted at Sintef’s Tiller facility in Trondheim. The Institute for Energy Technology (IFE) also contributed to developing the Olga and Volga tools for calculating this kind of flow. These models have eventually been adopted worldwide and still hold a dominant market share. Research was also conducted on how to avoid hydrate formation in the pipelines. Hydrates form when water and lighter hydrocarbons come in contact with each other under moderate to high pressure and in temperatures below 25°C. These conditions can produce ice-like crystals which may block wells, pipelines and process equipment.
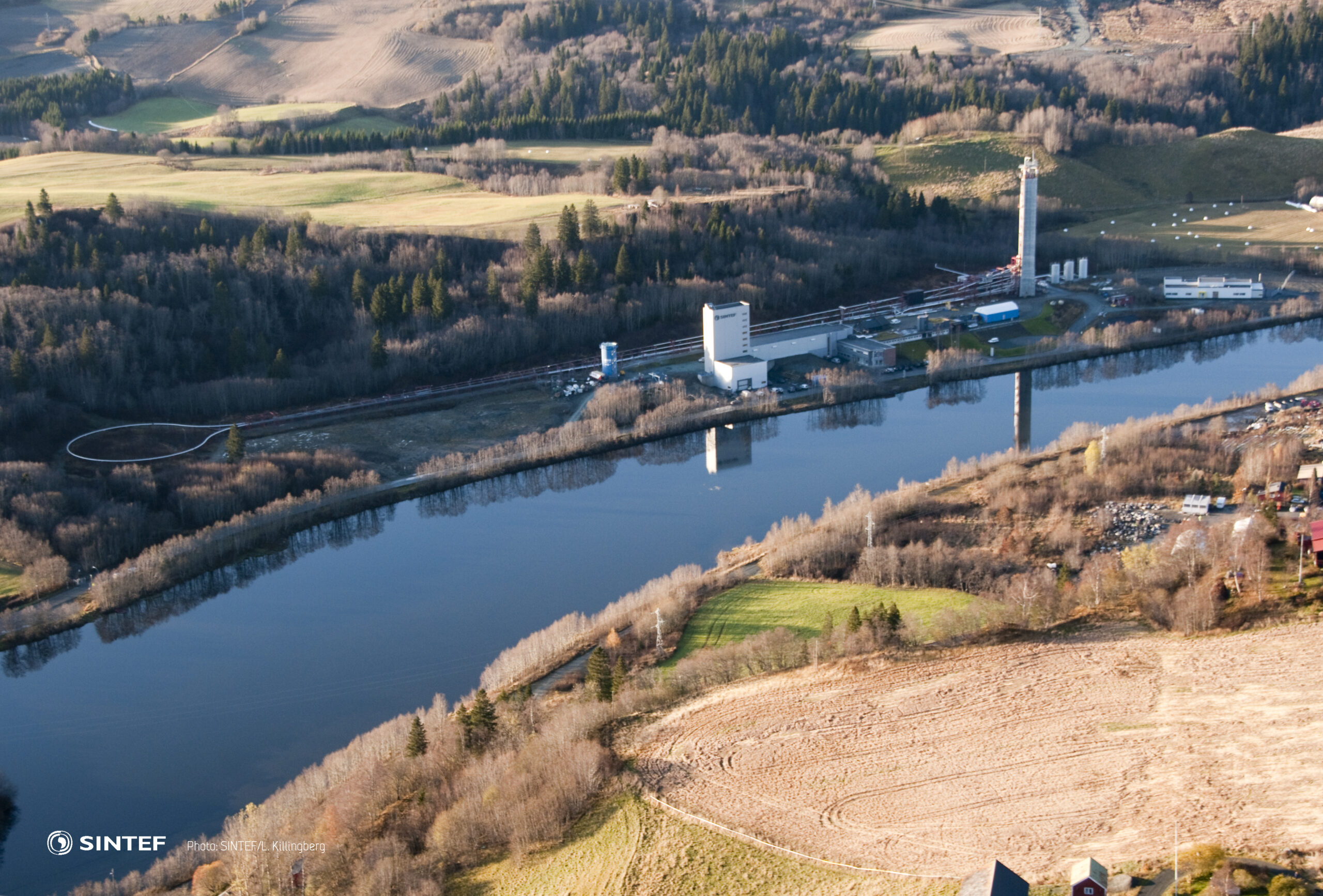
Statoil’s advanced position in research on material technology and multiphase flow was crucial for the Troll phase 1 concept. Instead of processing the wellstreams offshore, development operator Norske Shell – at Statoil’s initiative – opted to transport it as a multiphase flow directly to land. Only the water was separated on the Troll A platform, with gas and condensate being piped to the treatment plant at Kollsnes north-west of Bergen.
At a press conference in 1989, Shell announced that this solution would cut development costs by NOK 4.5 billion and trim NOK 330 million from annual running costs. Given a 70-year commercial life for the field, that adds up to a lot.
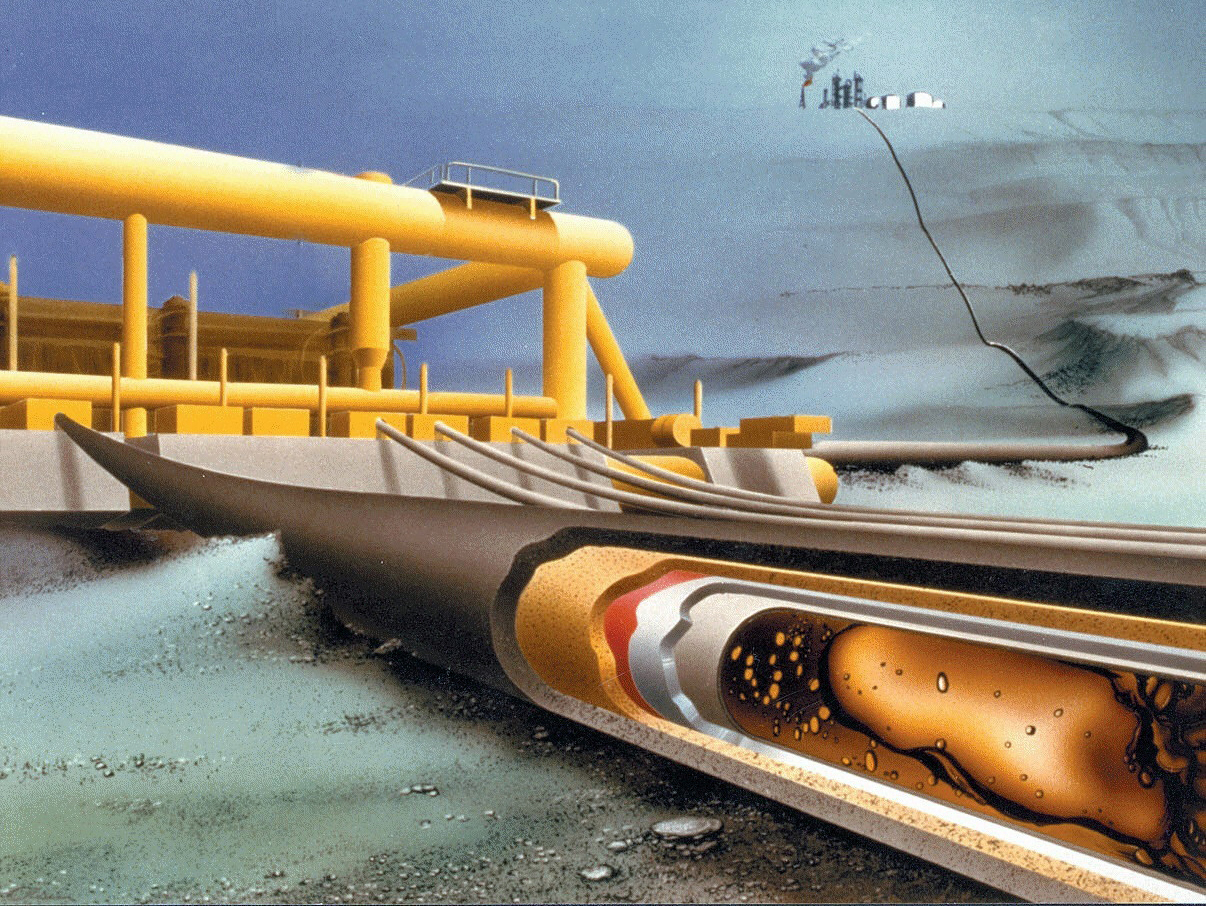
The first multiphase flow pipelines were laid in the late 1980s. In addition to the Troll A landfall solution, a crucial breakthrough was Norsk Hydro’s Troll Oseberg gas injection (Togi) project. These advances showed that such transport could yield big development savings while making marginal fields profitable. Discoveries which had not been commercial earlier could now be brought on stream with a subsea solution tied back to a process plant on land or on a nearby platform with spare capacity.
Two examples of a pure subsea solution without a fixed or floating platform are the Snøhvit and Ormen Lange gas fields, which both came on stream in 2007. Neither of these “subsea to shore” projects would have been possible without the results of multiphase flow research.
Floaters in deep water
Many discoveries were made during the 1980s on the Halten Bank in the Norwegian Sea, where water depths vary from 300 metres and beyond. Fixed platforms then became expensive. The only example of such a structure above the North Sea is on Draugen.
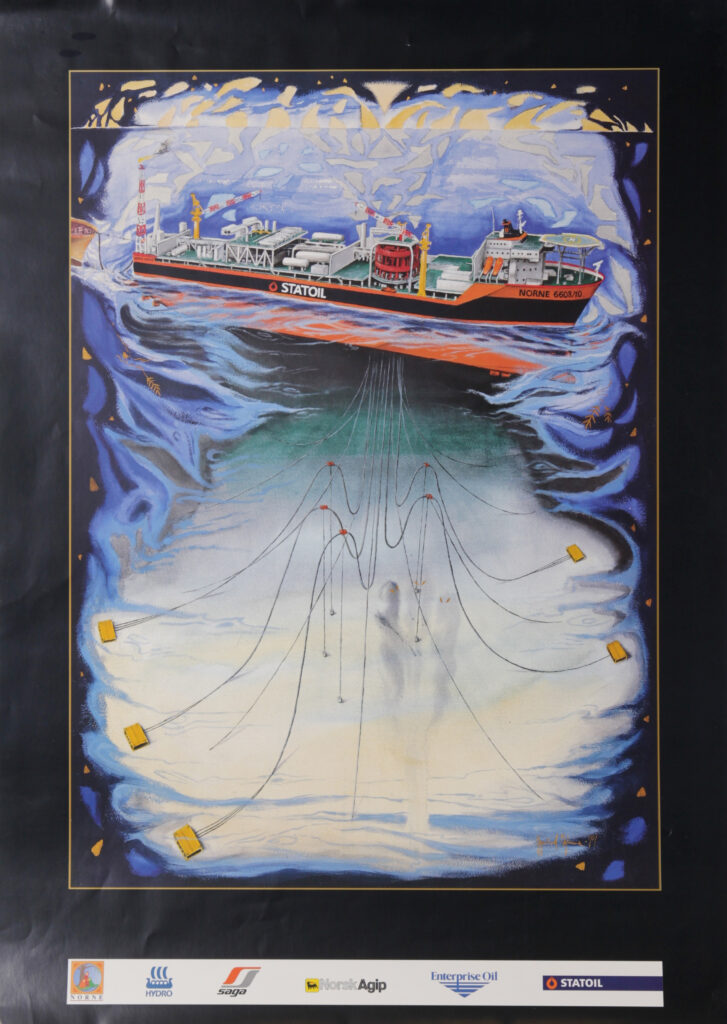
The alternative was floating installations. This represented pioneering work. Heidrun was approved for development in 1991 on the basis of a tension-leg platform (TLP) – a floater held to the seabed by steel tethers – plus a dedicated gas solution involving a pipeline to Tjeldbergodden in Norway and a methanol plant. The next projects in line were Statoil’s Smørbukk and Smørbukk South, Hydro’s Njord and Saga Petroleum’s Midgard. While both Njord and Smørbukk South could manage without a gas export solution for a number of years through injection back to the reservoir, Smørbukk and Midgard were wholly dependent on piping their gas south. Saga and Statoil found it difficult to come up with profitable solutions for the respective gas fields they operated.
Economics were not the only consideration. Feasible technical solutions were also needed for floating production installations. The capacity required for facilities on the Halten Bank was significantly greater than had been normal for production floaters until then. Other considerations included higher wellstream pressure and temperature as well as large motions for the installations because of winds and waves. The Smørbukk South licence had a development plan ready in 1992, but chose first to quality assure the swivel/turret technology required. On such vessels, flexible risers from the subsea wells enter via a rotatable cylinder or turret amidships which permits them to weathervane with the wind and waves without interrupting output.
This work gave the Norne project, also in the Norwegian Sea, a kick start the following year. The production ship concept chosen for this development was virtually a copy of that studied for Smørbukk South. Norne was Statoil’s first development based on a monohull floater tied back to subsea wells with the flexible risers required by vessel motion. This project proved a success in terms of both execution time, costs and quality. It also pioneered new ways of collaborating with the supplier industry.
Licence interests in the Smørbukk, Smørbukk South and Midgard fields were coordinated in a new unitised licensee structure with Statoil as operator. Named Åsgard, this ranks as one of the biggest-ever developments on the NCS with 63 production and injection wells in 19 seabed templates – the largest collection of subsea wells in the world at the time.
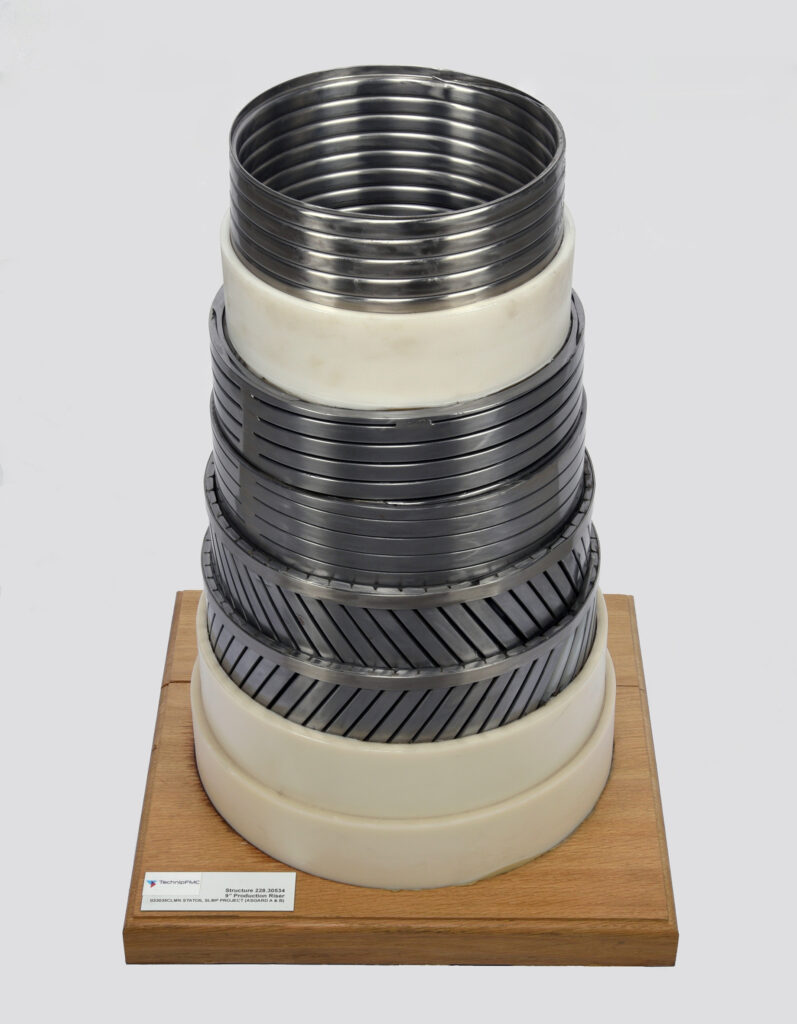
The project produces gas, condensate and oil from three very different and demanding reservoirs. Åsgard A was the world’s largest floating production, storage and offloading (FPSO) unit until then, while the capacity of the B platform made it the biggest floating gas processing facility. More than 20 comprehensive technology development programmes were pursued in parallel with the project. These included removing hydrogen sulphide from the wellstream, bundles of different types of pipe and signal cable in the same string, a pig launcher for pipeline cleaning, the swivel/turret, multiphase flow meters and flexible risers.
Throughout its producing life, Åsgard has functioned as a massive laboratory for hatching out, developing and adopting new ideas. Statoil’s own technology specialists, industrial partners and sub-contractors have developed and implemented world class innovations through projects for this field.
Significance for Statoil/Equinor
The technological progress which Statoil participated in on the NCS has proved very beneficial when the company has established itself in other countries with offshore oil production.
Operators in the Gulf of Mexico and on the Brazilian continental shelf have moved into steadily greater water depths than those encountered off Norway. Combined with technology advances on the NCS, this became crucial for the major developments in Angola and Nigeria which kicked off around 2000. Thanks to its technological commitment on the NCS, Statoil was then a welcome player in new deepwater areas – both as a participant in and operator for demanding field developments.
The basis for what can with hindsight be called a solid achievement was a conscious strategy to develop new technical solutions as well as a great willingness and, not least, the courage to include new solutions in its own projects in close collaboration with the supplier industry. That gave the company a competitive edge and a good reputation.
Where the Norwegian part of the petroleum industry is concerned, Statoil/Equinor’s willingness both to share new technical advances and to encourage and assist suppliers to develop intelligent new solutions have been crucial for the competitiveness built up globally by this sector over the past 20-25 years. Deliveries of technical solutions and services to the world oil industry rank today as Norway’s second largest export industry after oil and gas itself. That has created huge value for the owners and for Norwegian society.
Equinor now wants to continue as a leading energy and industry company in the “green shift”. It could then make sense to draw lessons from the recipe for success in such activities as technology development which initially made it a world leader in the petroleum sector.
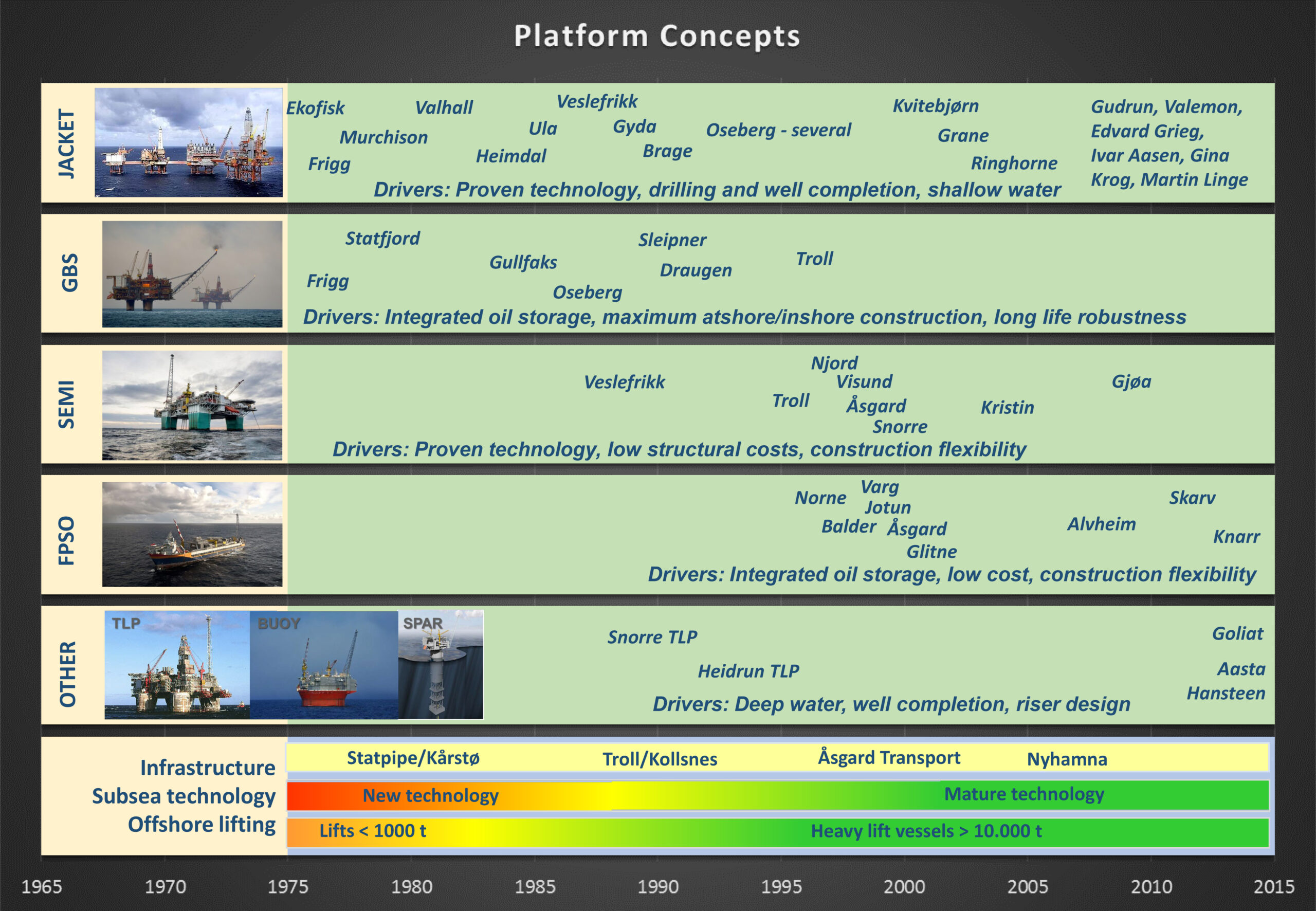