Statfjord satellites with fruitful industrial collaboration

Several nearby discoveries made in the Statfjord area during the 1970s could be produced via existing infrastructure. Statfjord East and North were proven in 1976-77 at distances of seven and 18 kilometres north-east and north of the C platform respectively. The first of these satellite fields lay in 150-190 metres of water, and the other in 250-290 metres. While both were smaller than the main field, their resources were nevertheless substantial and could increase overall Statfjord production by almost 15 per cent.
The question was how to develop them. Studies conducted as early as 1977-78 indicated that they were too small to bear the cost of their own concrete platform. A subsea solution would be best, but technology at the time was far from ready for such an application. Research and development (R&D) would be needed first.
Growing faith in subsea
Statoil participated with other oil companies in many research projects to overcome the subsea challenges presented by the Norwegian continental shelf (NCS).
During the 1980s, such work included determining how deep it was possible to dive. This was by and large a blind alley, and attention switched to technology which could eliminate the need for divers.
Statoil also took part in projects which made remote control of production wells possible over long distances.
And research was conducted into the way unprocessed mixtures of oil, gas and water from a well could be piped long distances over the seabed. Combined with testing, such work gradually increased confidence the subsea technology option for developing petroleum discoveries.
Statoil gained practical experience with underwater development on the Tommeliten and Gullfaks fields in 1986 and 1987 respectively. In these cases, choosing seabed wells saved both time and money. After a few years on stream, they also proved to operate very reliably.[REMOVE]Fotnote: Hans Jørgen Lindland by e-mail, 23 March 2021.
Developing the Statfjord satellites became relevant again in the late 1980s in order to help increase gas production sufficiently to secure a sales deal with continental Europe. Statoil’s subsea experts were convinced that underwater technology was the answer.
Arguing over technology
But the question was then which technical solution should be chosen. Several views were expressed, with Statoil and its partners – Mobil, Esso and Shell – arguing over the choice of development concept.
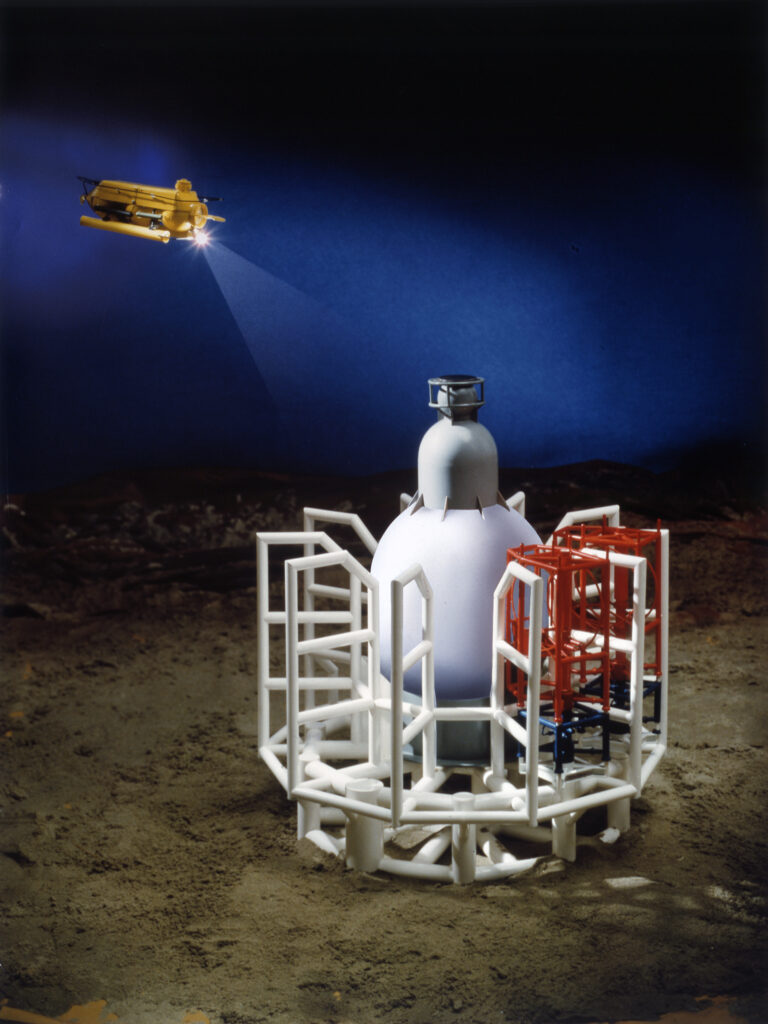
Mobil, which had been operator for Statfjord until Statoil took over in 1987, pinned much of its faith in the 1980s on seabed wells operating “dry” at atmospheric pressure. The technology had been under development in the USA since the early 1970s, and Mobil pushed hard for this subsea atmospheric system (SAS) to be used on Statfjord North. That would involve housing all seabed equipment in a habitat, so that repairs could made by personnel carried down in a submersible without diver involvement.[REMOVE]Fotnote: Annual report, 1986, Mobil: 18-19.
Given its experience of subsea wells, Statoil called instead for a solution with “wet” Xmas trees in an underwater production system (UPS) placed on the seabed.
The two companies reached a “gentleman’s agreement” on a combined solution, with Statfjord North developed using the SAS while the East satellite would be based on the UPS.
But Shell and Esso, the other partners in the licence, were dissatisfied with this. Realising both solutions would impose major R&D costs.
There were also grumbles from the Statoil team working on Statfjord North. Experience with the Gullfaks satellites showed that subsea developments required no people under water. The SAS required operators down on the seabed. Underwater working was not only risky for personnel in itself, but had to be done in a cramped space while operating equipment controlling oil and gas flows under high pressure, with the hazards that this involved.
Scepticism about the SAS was fully supported in the licence by Shell, which was operating without diver assistance on its Draugen development in the Norwegian Sea. Esso, for its part, used every opportunity to say that it wanted state-of-the-art subsea systems rather than testing new technology. It preferred similar systems on Statfjord North and East rather than different technological solutions. Much could be gained financially from such standardisation.[REMOVE]Fotnote: Hans Jørgen Lindland in conversation with Kristin Øye Gjerde and Arnfinn Nergaard, 21 October 2016.
KV’s smart solution
Through its Gullfaks satellite project, Statoil had developed good contacts with the subsea department at Norway’s Kongsberg Våpenfabrikk (KV). The latter had learnt what the oil company wanted, including overtrawlable wellheads to avoid problems with the fishing sector. And it should be possible to install and operate a system without diver assistance. Such insights proved beneficial when Statoil requested tenders for a subsea solution on the Statfjord satellites.
This invitation coincided with an inquiry from Shell concerning seabed installations to be used for its Draugen development. KV saw the chance to produce subsea wells for both projects using a more or less identical concept. That allowed it to offer a far lower price than its competitors. The company won the two jobs, and both the SAS and the UPS were rejected.[REMOVE]Fotnote: Tore Halvorsen interviewed by Kristin Øye Gjerde and Arnfinn Nergaard, 18 October 2017.
The plan for development and operation (PDO) for Statfjord North and East was approved by the Storting (parliament) on 11 December 1990. That allowed Statoil to sign the contract with Kongsberg Offshore Systems (KOS), as the company was then called.
Development costs down
KOS was a turnkey contractor, which meant that it handled design, equipment production in-house and by subcontractors, and installation on the field.
When designing the system, great emphasis was placed on the ease of connecting up the various components on the seabed. The seabed template was configured so that technical equipment was built into replaceable modules.
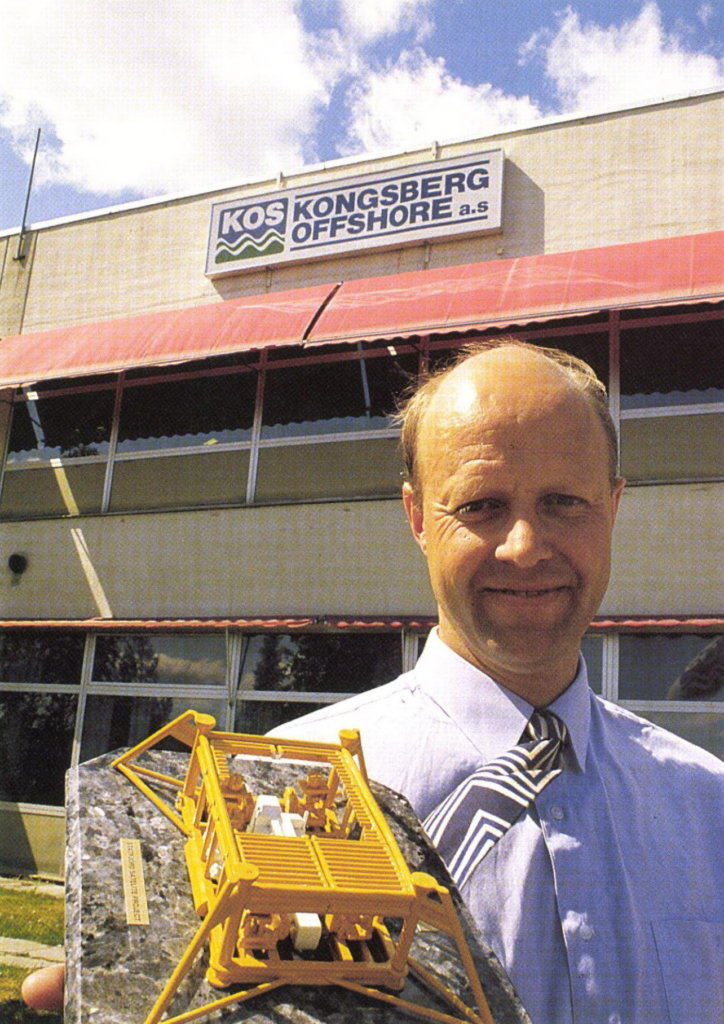
KOS delivered two production templates and one for water injection for each of the Statfjord satellites. That added up to six structures providing 18 well slots. The wellstream was piped to Statfjord C for processing, storage and export.[REMOVE]Fotnote: Daling, Unn Kristin and Erlandsen, Hans Christian, Offshore Kongsberg 25 år, 1974–1999, 1999: 150-51.
The subsea system could be operated from a rig or a ship. It comprised a tool frame and a lifting arrangement, and the operator controlled a remotely operated vehicle (ROV) and tool (ROT) for inspecting and replacing components. The ROV was generally sent down first to film, giving the operator a good overview of the actual job.
All the underwater equipment was designed for diverless installation, operation and maintenance. That fitted well with Statoil’s goal of eliminating the need for diver assistance by 2000.[REMOVE]Fotnote: Henrik Carlsen in conversation with Arnfinn Nergaard and Kristin Øye Gjerde, 27 January 2017. It was also a step towards overcoming the challenges of working down to 1 000 metres, which Statoil envisaged for the future.[REMOVE]Fotnote: NUTEC Dykkenytt, no 4/1995; Statoils undervannssystemer, about 1993, brochure.
An advantage of the templates with subsea Xmas trees was that, once installed, they could be brought on stream quickly. That contributed to a solid reduction in development costs per well over the decade after 1986. Each well on the Gullfaks A platform had cost NOK 170 million. That was down to NOK 85 million for the Statfjord satellites in 1992.[REMOVE]Fotnote: Statoil memorandum, 1998, “Viktige beslutninger for UTV-området i Statoil”.
A couple of years later, KOS introduced fold-out templates which were so compact that they could be lowered through the open well (moonpool) on a mobile drilling rig. This hinge-over subsea template (Host) cut the development cost per well drilled to NOK 30 million in 1996.
Among the discoveries to benefit from Host was the Sygna satellite on the northern flank of Statfjord, which was sanctioned for development in 1996 with two of these modules. The contract went to KOS, which had become FMC after being taken over by the US company of that name.
Operating reliability, standardisation and price reductions were to the oil companies’ taste, and a number of fields on the NCS were developed with subsea wells during the 1990s. Norway’s Statoil, Norsk Hydro and Saga Petroleum companies were leaders in being willing to try out and continue developing underwater technology. It also became normal to pipe oil and gas from the wells to a production floater rather than a fixed platform.
Government praise
When the Statfjord satellites were officially inaugurated on 9 June 1995, Statoil and the supplier companies could be proud that this development had moved some technological boundaries. That included a new distance record for piping an unprocessed wellstream over the seabed to the processing platform.
Indeed, the whole technological leap which took place on the NCS in the 1980s and 1990s was sensational. It was characterised by a close collaboration between KOS with its subcontractors and Statoil as the client, and between other licensees.
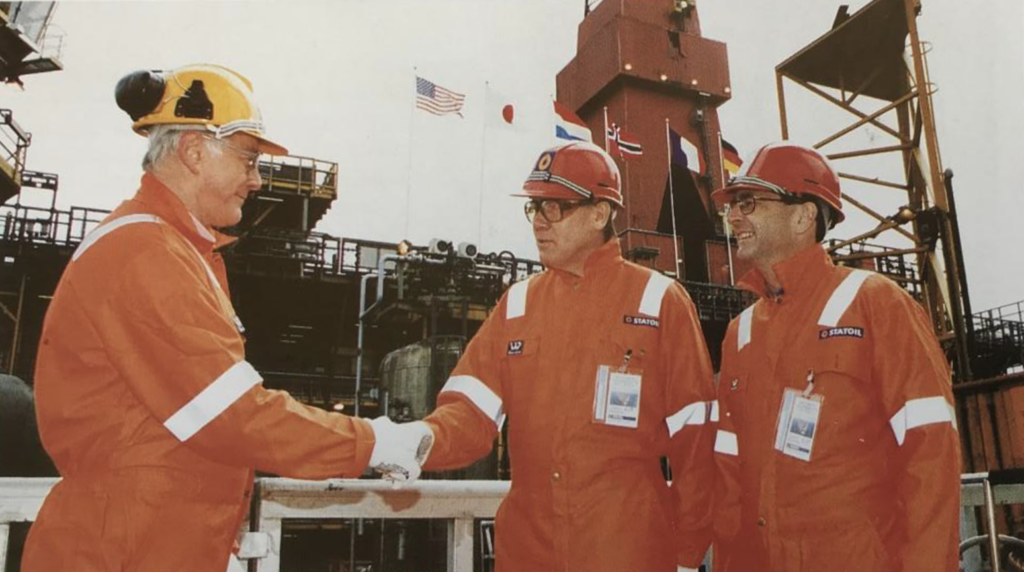
This was viewed as constructive by the government. Labour’s Gunnar Berge, then minister for local government and labour, commented in his inauguration speech for the satellites on the positive way Statoil had adopted a long-term form of collaboration with KOS. That laid a good basis for future deliveries and continued development both on the NCS and internationally.[REMOVE]Fotnote: Gunnar Berge, minister of local government and labour, official inauguration of the Statfjord satellites on Statfjord C. That was no doubt particularly satisfying to hear for the Kongsberg team, which had participated in finding the solutions and was on its way to setting a standard in subsea technology.
According to Tore Halvorsen, the then CEO of FMC, huge interest was being shown in Norway by the USA, Brazil and later Australia. Much of the technology was innovative and Norwegian-developed. Doing without diver assistance, utilising manifolds and pulling-in flowlines horizontally were all new. Norway’s subsea industry gained a huge boost. FMC’s head office in Houston allocated many new areas of responsibility to Kongsberg and the Norwegian milieu.[REMOVE]Fotnote: Tore Halvorsen by e-mail, 23 February 2021. Much of this was thanks to the contracts the company had secured from Statoil.
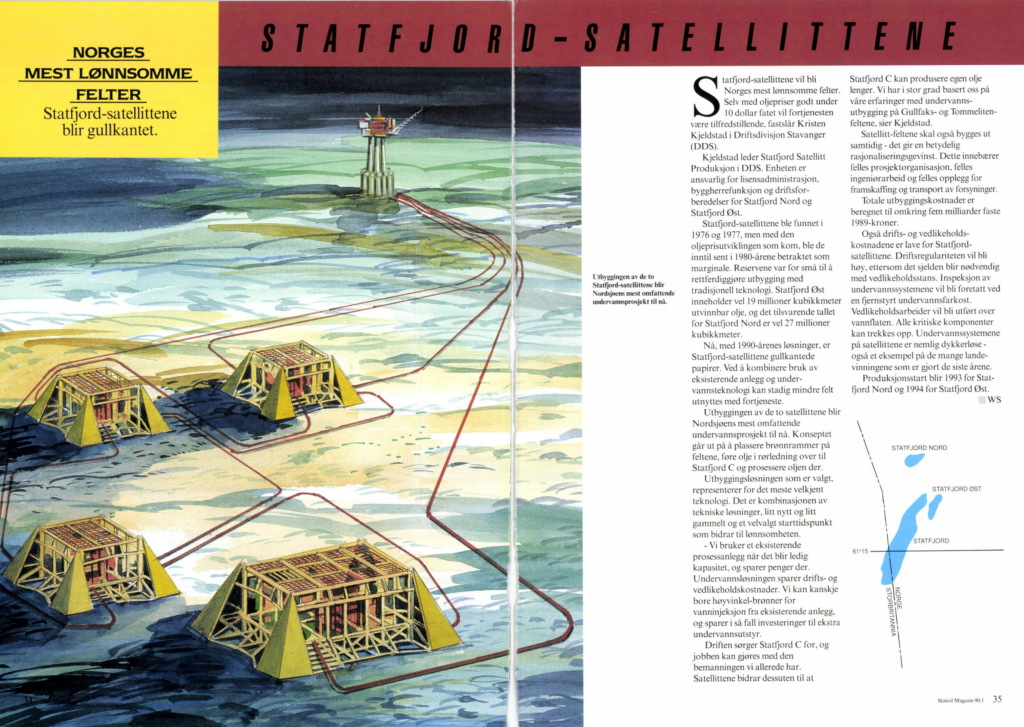