Norway’s most profitable invention

The Olga story started in the summer of 1980, when Knut Åm –Statoil’s first technical vice president – was visited by two scientists who needed help to turn an idea into reality. This meeting with Kjell Bendiksen and Dag Malnes from Norway’s Institute for Energy Technology (IFE) led to support being provided to develop a computer programme.
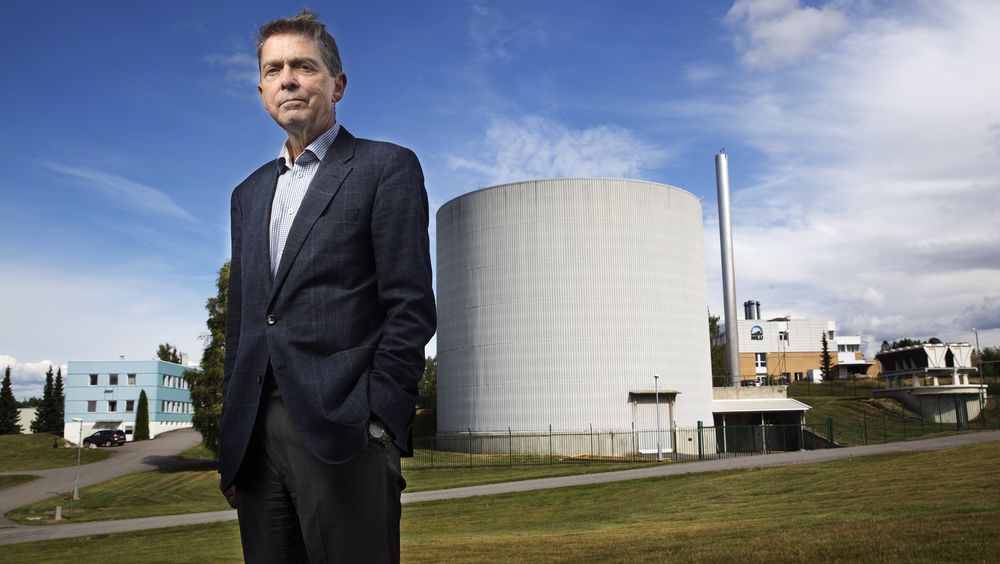
The challenge this was intended to overcome concerned piping unprocessed mixtures of oil, gas and water from a seabed well to a platform some distance away. Such multiphase flow ran the risk of water ice and hydrates (a kind of hydrocarbon ice) forming in the pipeline and causing problems. The computer model was intended to calculate how much “anti-freeze” had to be added to prevent this happening, which depended in turn on the composition of the pipeline flow. It was dubbed Olga from a contraction of the Norwegian terms for oil and gas (OLje and GAss), based on a suggestion from Bendiksen’s wife the evening before the meeting with Åm.[REMOVE]Fotnote: Dagens Næringsliv, 26 January 2018, “Forskerne som formet hver sin bit av Norge”.
Cost cuts sought
The first developments on the Norwegian continental shelf (NCS) – Ekofisk, Frigg and Valhall – occurred in relatively shallow water utilising technology developed in the USA.[REMOVE]Fotnote: This article builds to a great extent on chapter 5 of Getting Down to It. 50 Years of Subsea Success in Norway, 2019, by Kristin Øye Gjerde and Arnfinn Nergaard.
As large discoveries were made in steadily deeper water, they were exploited with huge concrete platforms based on the Condeep design developed in Norway. But these monsters were expensive. The Statfjord development experienced big cost overruns, which generated a great deal of political noise in the second half of the 1970s. The government appointed a special commission of inquiry chaired by professor Johannes Moe at the Sintef research institute to investigate opportunities for cutting development costs.
Good ideas which could make offshore projects less expensive were welcome. This was where Bendiksen and Malnes came in. They argued it was possible to make them simpler. Rather than installing large processing plants on platforms to separate the oil, gas and water phases, anti-freeze could be added to the unprocessed flow from subsea wells. They could then be piped – in the ultimate analysis – to a plant on land. On a smaller scale, wellstreams from satellite fields could alternatively be transported to the nearest platform with processing facilities.
Åm listened with interest, because such a solution could be used on Statfjord, for instance. Two relatively large satellites – Statfjord East and North – had been discovered there in 1976-77. These lay in 200 and 290 metres of water respectively and at distances of several kilometres from the installations on the main field. The Statoil executive wanted to know whether it was possible to develop and operate these two without more big Condeeps, using subsea wells producing directly to an existing platform.
Multiphase challenges
As long as petroleum has been produced, multiphase mixtures of oil, gas and water emerging from a well have been carried by pipeline before processing. When production takes place offshore, problems arise which increase in severity the greater the distance, the deeper the water and the colder the ambient temperature involved.[REMOVE]Fotnote: For a good and detailed review of the background for and utilisation of Olga, see Nygård, Pål, Controlling the flow of oil and gas subsea.pdf. That is because the properties of the wellstream components differ with pressure and temperature, so that each of them behaves in their own way when piped over long stretches.
When flowing up the well, the oil/gas/water mix – along with sand – is warm from geothermal heat and well blended. At pipeline level, its pressure falls and the gas phase expands to take more space. As it then passes along the pipeline, the mix is cooled down by the surrounding cold water – which can be close to 0°C at the seabed in deep waters. The properties of the wellstream therefore change even more, and chemical reactions take place along the whole length of the pipeline. These can find expression in many ways.
Small changes – in the angle of the pipeline, for example – can have large effects and be crucial for such transport properties as liquid quantity, stability and pressure drop. Where the pipeline bends upwards, in particular, so that the flow slows down, water and oil can accumulate as liquid plugs – or “slugs”. Pressure builds up behind these, increasing their speed and producing big forces which can cause damage to the pipeline, the riser to the platform, and the topside receiving facilities.[REMOVE]Fotnote: Bendiksen, Kjell, “Hvordan bidro FoU og OLGA til Norges ledende posisjon på undervannssystemer for flerfasetransport av olje og gass?”, paper, 2016.
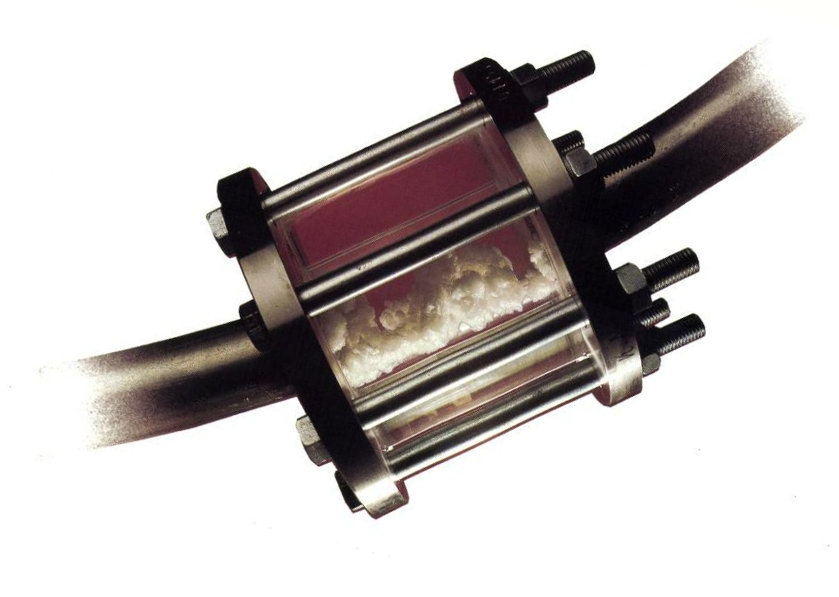
To avoid this, the engineers designed very robust devices on the platform known as slug catchers. These were dimensioned to withstand the force of the liquid “punches”. Another risk was the formation of hydrates, solids which could be damaging for the pipeline and difficult to dislodge. All in all, the wellstream flow can vary. At one point, it can be layered, with water and oil at the bottom and gas on top, and moving smoothly. Elsewhere it can look like a chaotic mess of oil, gas pockets, water droplets and long slugs.
The oil companies therefore needed reliable models for calculating and analysing what was happening in the pipeline at any given time. That would then allow them to take countermeasures to prevent plug and hydrate formation, and eliminate the requirement for big and costly slug catchers. They also needed to know how often a pipeline had to be “pigged“ – cleaned by pumping through devices known as “pigs” to remove wax and other deposits. The Olga tool was intended to meet these requirements by helping to calculate risk. The more the oil companies knew, the better the economics of their developments.
From nuclear physics to wellstreams
Bendiksen, who had a background as a nuclear physicist in an international research community,[REMOVE]Fotnote: Via the IFE, Bendiksen secured a job in the OECD’s Nuclear Energy Agency (NEA) – first two years at Euratom’s Italian research centre, and then a year at France’s CEA nuclear energy institute at Saclay, about 20 kilometres south of Paris. hit on the idea of the Olga model together with Malnes at the beginning of 1980. At the time, nuclear power was all the rage in Europe and many facilities for generating this form of energy had been built since 1945. Norway had also been conducting nuclear research at the IFE, which had reactors at Kjeller and Halden in the south-east of the country. However, all such work was shelved in the 1970s because of strong political opposition. The oil age beckoned instead.[REMOVE]Fotnote: Teknisk Ukeblad, 14 October 2018. https://www.tu.no/artikler/kjell-bendiksen-hydrogenproduksjon-fra-naturgass-er-det-eneste-realistiske-alternativet-for-a-na-klimamalene/448588 And, with multiphase flow an important issue in this sector, knowledge gained from nuclear power plants proved transferrable to the petroleum industry.
Over the years, the IFE had developed computer tools to simulate the flow of water and steam (two-phase) through nuclear power stations. Creating Olga could draw on this work. The model was adapted to the pressures and viscosities (flow resistance) which applied to oil and gas in pipelines, and a “zero” version was ready in June 1980. It was tried out physically by sending a multiphase mix through a pipeline on land in a test station at the University of Tulsa in the USA, and proved astonishingly successful.
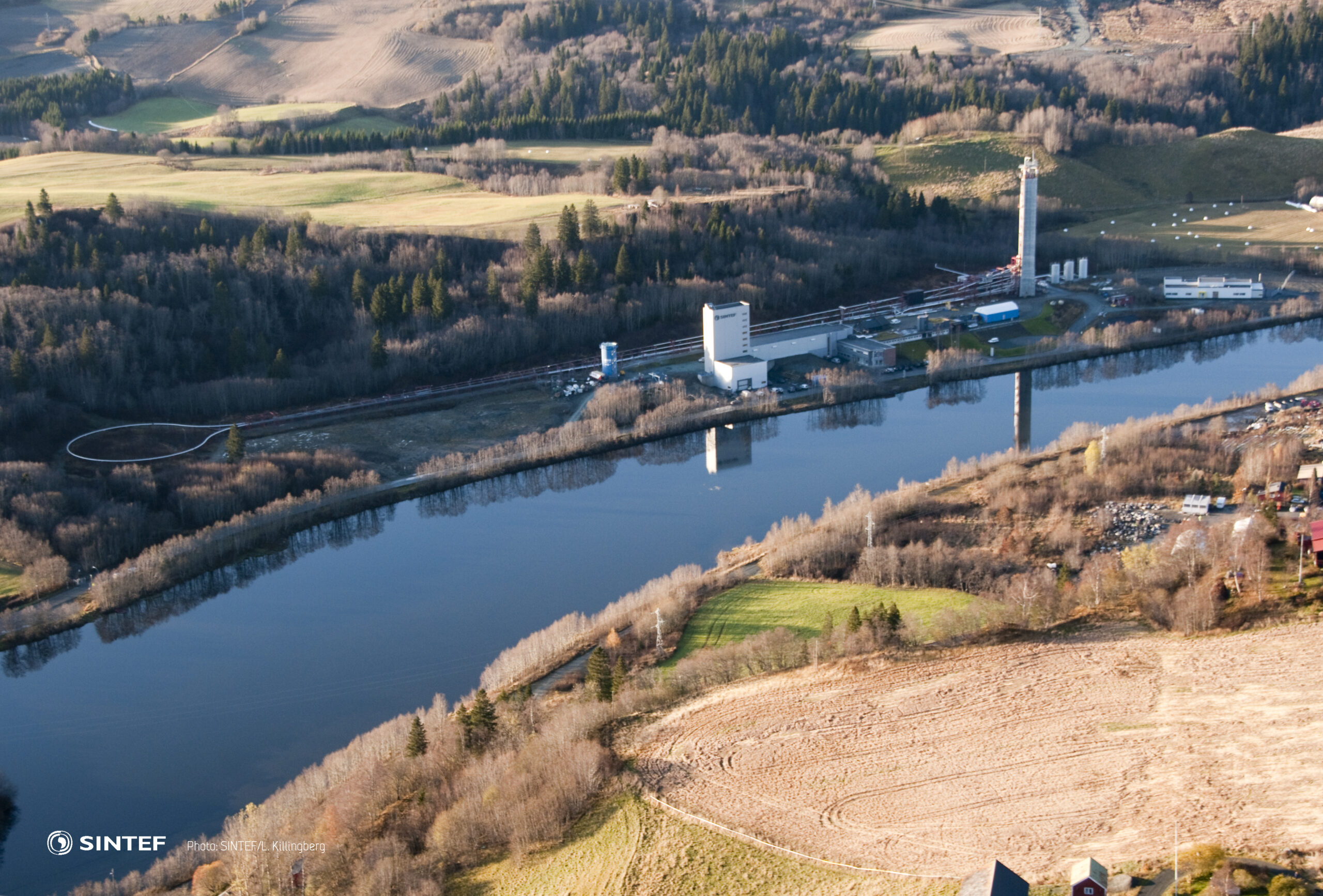
To be used out on a field, however, Olga had to be tested and verified experimentally in a much larger facility. Hence the visit to Åm, which convinced him that this was a viable concept. Statoil funded Olga development at the IFE for the next four years.[REMOVE]Fotnote: Bendiksen, Kjell, op.cit. It therefore fitted very well that Esso was ready in 1980 to finance the construction of a multiphase flow test plant under its goodwill agreement with the Norwegian government. Entered into by foreign oil companies in 1979-93 in order to qualify as applicants for offshore licences, these deals covered the funding of petroleum research and development in Norway.[REMOVE]Fotnote: Gjerde, Kristin Øye and Nergaard, Arnfinn, 2019, Getting down to it. 50 years of subsea success in Norway: 78.
The multiphase flow facility was installed at Tiller south of Trondheim and imitated a full-scale installation in the North Sea. It incorporated a 52-metre-tall concrete tower topped by a separator and a 1 000-metre-long horizontal tubular section. This allowed scientists to see how two-phase mixtures of gas and water behaved and whether the calculations made using computer models matched reality.[REMOVE]Fotnote: Norsk Olje Revy, no 6, 1980, “Forsøksanlegg for to-fase-strømming skal bygges i Trondheim.”
When the facility was inaugurated on 25 January 1983 by petroleum and energy minister Vidkunn Hveding, it had cost some NOK 80 million.[REMOVE]Fotnote: Moe, Johannes, Norsk Oljemuseums årbok, 2011. Funding came from Statoil, Mobil, Texaco and Getty Oil in addition to Esso.[REMOVE]Fotnote: Norsk Olje Revy, no 6-7, 1982, “Two-phase flow facility nears completion”. Sintef took over the test station on 1 February 1984.[REMOVE]Fotnote: Flyt. Flerfasetransport på sokkelen i 25 år, 2009, brochure published by Sintef and the IFE.
A smaller test unit was also built at the IFE, comprising a 20-metre pipeline section with a diameter of 0.1 metres. The first 10 metres were in stainless steel, followed by two five-metre sections in transparent PVC. This set-up could be given an inclination of up to 20 metres, and made a substantial contribution to increasing knowledge about multiphase flows.
Successful collaboration
According to Bendiksen, a big need – a craving – existed in the industry for completely new solutions on the NCS. The oil companies were ready to adopt them as soon as they were available. That Statoil, Esso and Hydro were all seeking new solutions based on multiphase flow in the early 1980s for their big gas fields helped to build up strong R&D teams in Norway. Funding for the research programme was spread even more widely from 1984, with no less than nine oil companies joining forces in a big joint industry project worth NOK 40 million for 1984-86.[REMOVE]Fotnote: Computerworld, 14 February 2014, “Flerfase gir milliardbesparelser”.
The IFE-Sintef collaboration also embraced the Norwegian University of Science and Technology (NTNU). In collaboration with the supplier industry, multiphase flow issues were gradually understood and solutions adopted in practice. That included tests on the Tommeliten field in the North Sea.
In 1986, Total and Statoil signed a new research agreement known as Poseidon II. This joint commitment provided NOK 25-30 million a year up to 1993 for 10-15 scientists to work full-time on multiphase flow.[REMOVE]Fotnote: NTB, 4 December 1987, “Total og Statoil med ambisiøst forskningsprosjekt”. Statoil had by then established its own research centre at Rotvoll in Trondheim, whose specialists collaborated with the scientists at the Tiller facility.
Freezing of water and liquid plug formation were the focus of attention in Poseidon II. That included research on pump systems, new materials in pipelines and innovative instruments.[REMOVE]Fotnote: NTB, 3 March 1988, “Ny oljeteknologi skal gi milliardgevinster”. Olga was commercialised through Scandpower (STC Group) in 1989.
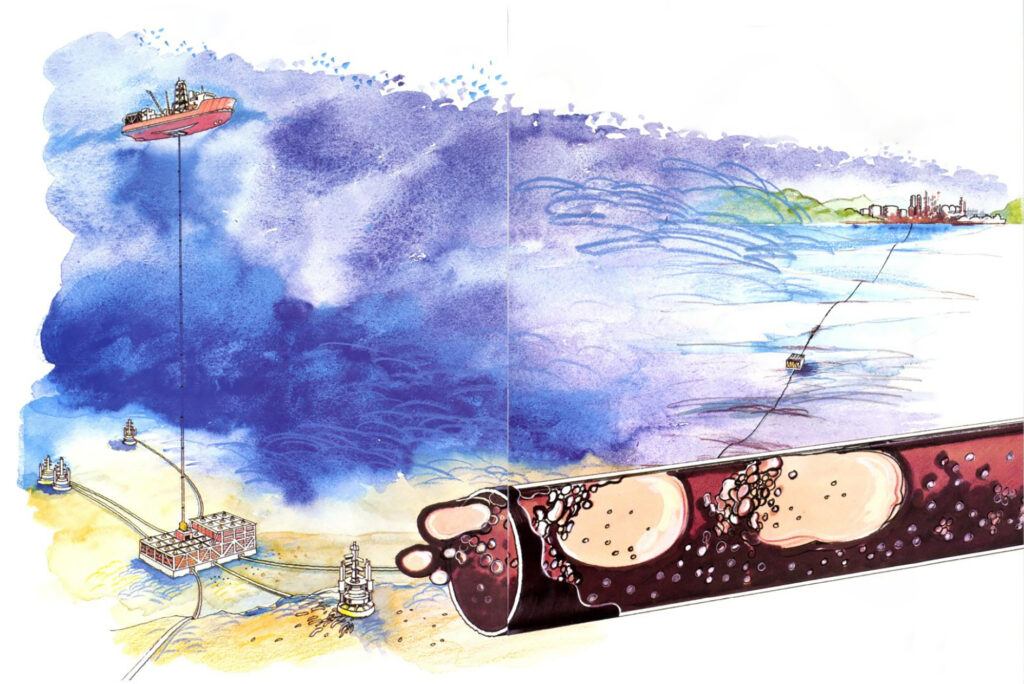
It became known in 1991 that Statoil would continue the research programme. The company provided an annual grant of NOK 400 million to Sintef and the IFE for five years to fund the work of about 60 scientists. The company had several potential subsea projects which would depend on multiphase wellstream flow to become financially viable. That included the Statfjord satellites, Troll and Snøhvit.[REMOVE]Fotnote: Aftenposten, 27 November 1991, “Forskningsprosjekt til 2 milliarder”. Such a far-sighted commitment put Norway well up with the front runners in international multiphase-flow research and technology. The scientists involved have won a number of prizes for their work.
World-class results
Multiphase flow technology is one of the cornerstones for subsea production, and has formed the basis for the continued development of solutions for subsea wells. Modelling such transport has contributed to the emergence of a Norwegian supplier industry for subsea equipment, such as Xmas trees, which also has an international market.
Advances with multiphase flow have made it possible to develop a number of fields more effectively and profitably, as well as discoveries which would otherwise have remained unproduced. It would otherwise hardly have been possible to develop Snøhvit and transport its unprocessed wellstream 143 kilometres to land, or Ormen Lange in 1 000 metres of water. These are just the most extreme examples of how useful Olga has been for the NCS.
arrow_backNorthward bound – with high hopesOffshore employers come togetherarrow_forward