Teknologiutvikling i Statoil

I all industri vil utvikling og effektiv bruk av ny teknologi være av stor betydning for å øke konkurransekraften og for å møte nye krav og behov fra kundene. Men introduksjon av ny teknologi, eller ny bruk av etablert teknologi, medfører alltid en viss risiko. Vegen fra idé til vellykket bruk går derfor som regel via en detaljert gjennomgang og analyse av forretningsideen, utprøving i mindre skala (eventuelt laboratorieforsøk) og en fullskalatest (hvis mulig). Hvordan har dette artet seg i Statoil/Equinors bruk av ny teknologi?
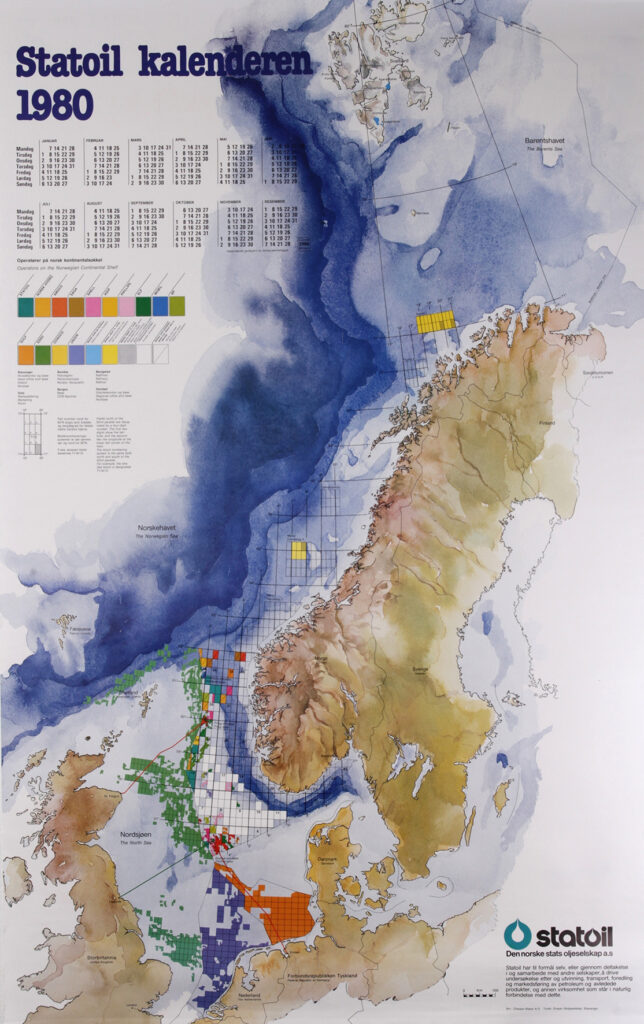
Gunstige forutsetninger
I 1972 ble Statoil og Oljedirektoratet (OD) etablert. Helt fra starten av var det et mål at Statoil skulle være et integrert oljeselskap med formål å bli en operativ virksomhet innen hele verdikjeden fra leting via utbygging, produksjon til salg av produkter.
Statoil startet sin oljevirksomhet på et gunstig tidspunkt. Teknologier som gjorde det mulig å bore brønner og produsere olje fra plattformer på havdyp på inntil 100 meter, var relativt ferske. De var utviklet i USA siden slutten av 1940-årene, og ble importert til Norge fra da den første leteboringen startet i 1966. Dette gjorde det mulig å lete etter olje og gass i den relativt «grunne» sørlige delen av Nordsjøen, hvor gigantfeltet Ekofisk ble påvist i 1969 og gassfeltet Frigg i 1971.
I Norge var det fremsynte politikere som etablerte klare målsettinger for den nye industrien, inkludert krav om norsk innhold, deltagelse og kontroll. Embetsverket etablerte profesjonelle rammer og retningslinjer for industrien. Den «norske modellen» ble utviklet med tydelig ansvars- og rollefordeling mellom Storting og departement, tilsynsorgan (OD), og oljeselskapene (Statoil og andre).
Norsk leverandørindustri kunne dra nytte av sin kompetanse innen maritim virksomhet (for eksempel ved utviklingen av Akers boreplattform H3), skipsbygging (for eksempel Kværners gasstankere) og anleggsvirksomhet (for eksempel bygging av betongdammer og broer). Krisen i tankskipsfarten i 1970-årene førte til en omlegging fra skipsverft til offshoreverft. Dessuten økte oljeprisen kraftig i 1970-årene både på grunn av økende global etterspørsel etter olje og gass og politisk uro i Midtøsten. Den økte oljeprisen bidro til at Statoil kunne utvikle seg til et selskap som fant løsninger på de særegne utfordringene på norsk sokkel, med store vanndyp og tøffe klimatiske forhold.
Statpipe og betongplattformer – første trinn på teknologistigen
Et av Statoils viktigste felt, Statfjord, som ble påvist i 1974, ligger i Tampen-området. Der varierer vanndypet mellom 120 og 250 meter. Planlegging av ilandføring av gass fra Statfjord var det første prosjektet Statoil tok på seg et utredningsansvar for.
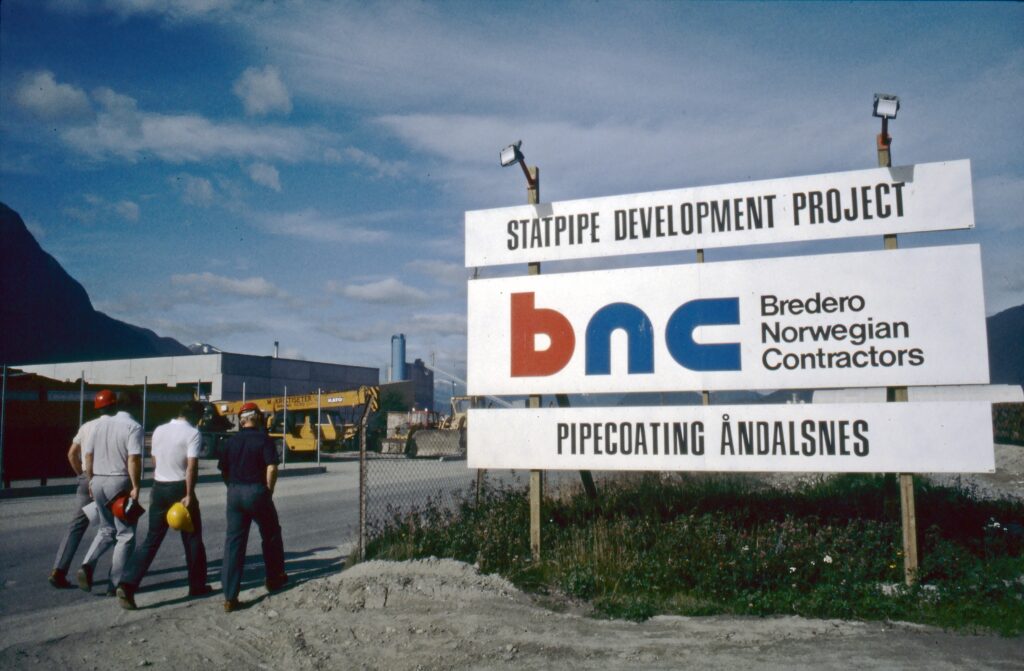
Myndighetenes krav var at olje og gass fortrinnsvis skulle ilandføres til Norge for å sikre maksimal verdiskapning for landet. Mellom Tampen og Vestlandskysten ligger Norskerenna med sin dybde på 3–400 meter, som var et utfordrende hinder med en rekke uløste teknologiske problemstillinger. Utredningsprosjektet som startet i 1976, ble en viktig forløper for utbyggingen av Statpipe/Kårstø og også for den ledende posisjonen selskapet etter hvert fikk for både installasjon og drift av offshore-rørledninger.
På plattformsiden ble personell fra Statoil utlånt til og innlemmet i Mobil sine prosjektorganisasjoner på Statfjord. Mobil sitt konseptvalg for Statfjord var tre betongplattformer med integrerte dekk som inneholdt prosessering, borefasiliteter og boligkvarter (PDQ). Fordelene med betongplattformer var mange:
- De egnet seg for vanndypet på Tampen
- De hadde lang levetid og kunne understøtte et dekksanlegg på 50-60 000 tonn
- Mesteparten av arbeidet kunne ferdigstilles ved land
- Et stort oljelager kunne innlemmes i konstruksjonen
- Norsk industri hadde god kompetanse på betong
- Betongplattformene kunne bygges lokalt i Norge
Planlegging og gjennomføring av Statfjord-utbyggingen sammen med Mobil ble særdeles viktig læring for Statoil. Blant annet ble det utviklet nye og effektive bøyelastingssystemer til bruk offshore.
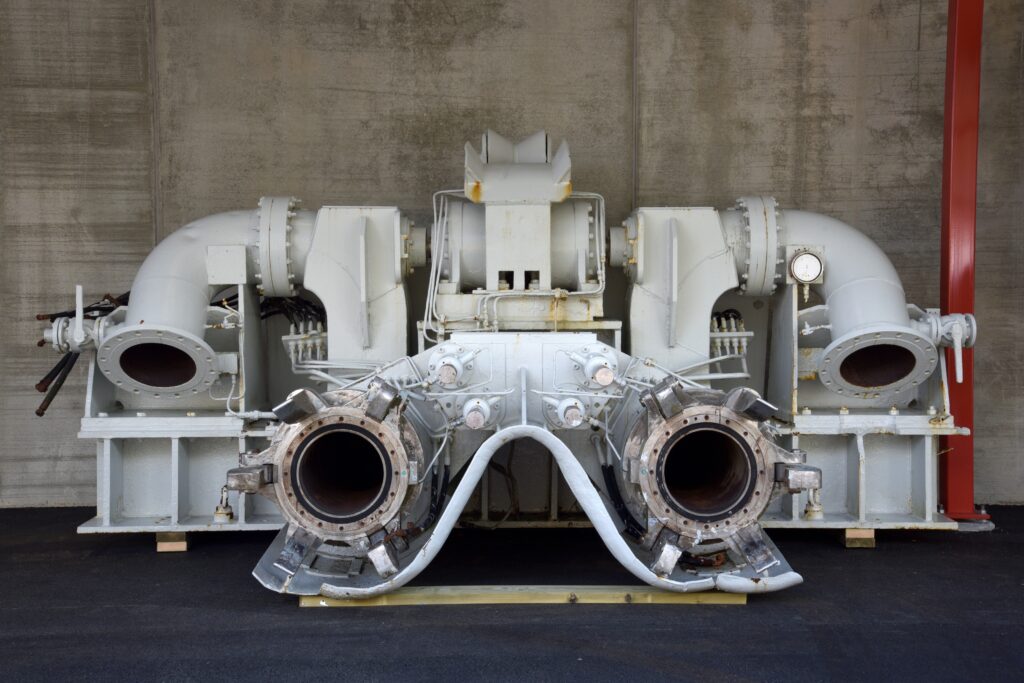
Statoil ble etter hvert ledende på norsk sokkel innen rørtransport av gass og olje. Statpipe var i sin tid verdens lengste offshore-rørledning. Utfordringene med Norskerenna ble løst og det ble utviklet teknologier for reparasjonsmetoder for vanndyp ned til 360 meter, der dykkerne arbeidet inne i et kammer fylt med nitrogen og dermed ikke var eksponert direkte for sjøvann. Mer effektive metoder for nedgraving og beskyttelse av offshore-rørledninger ble utviklet.
Siden det var åpenbart at det ville bli behov for reparasjon av rørledninger på enda dypere vann på norsk sokkel, ble et stort utviklingsprosjekt igangsatt for å finne metoder for å utføre rørsammenføyning og reparasjon av rør helt uten bruk av dykkere.
Et annet område Statoil bidro sterkt til, var forskning innen maritim materialteknologi. Behandling og transport av korrosive brønnstrømmer i et røft maritimt miljø byr på mange utfordringer og overraskelser. Statoil etablerte materiallaboratorier både i Stavanger og senere i Trondheim som fikk stor betydning for valg av materialer til nytt utstyr og løsninger.
Gullfaks på norsk
Statoils første operatørrolle var på Gullfaks, som også ligger i Tampen-området. Etter konsesjonstildeling i juni 1978 ble første funn gjort en måned senere. Planlegging av første fase av utbyggingen startet tidlig i 1980. Utbyggingssøknad ble sendt til myndigheten på slutten av året og vedtatt av Stortinget i juni 1981. Gullfaks ble Statoils første storskala-laboratorium for utvikling av flere teknologier.
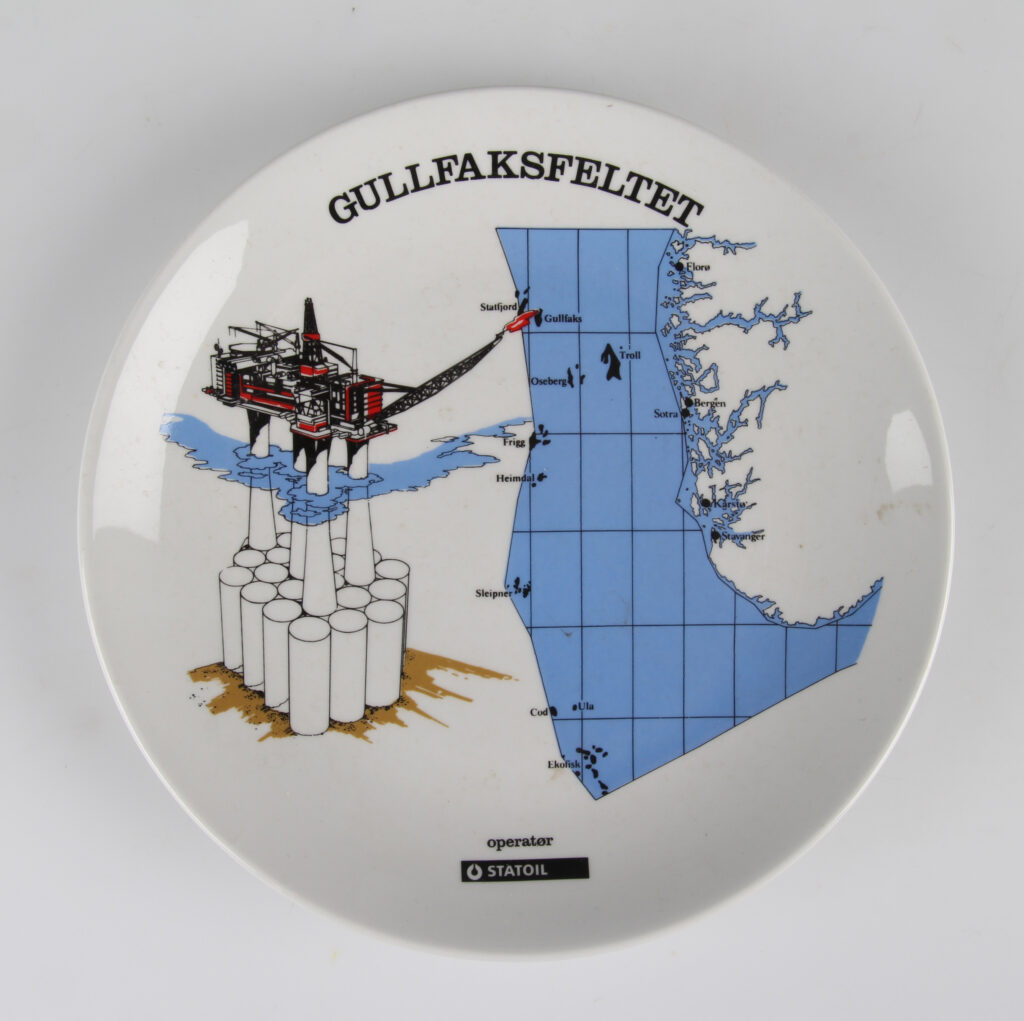
Utbyggingens første fase omfattet to store anlegg til havs, Gullfaks A og B, med tilhørende lastebøyer. Dette var første gang et felt ble bygd ut med bare norske eiere, norsk operatør, norsk arbeidsspråk og i all hovedsak norske leverandører. Hele 80 prosent av kontraktene på de to plattformene gikk til norske selskaper. Gullfaks A gikk inn i et svært tett samarbeid med norsk industri hvor MVL (Mekaniske Verksteders Landsforbund) var den aller viktigste samarbeidspartneren.
Prosjektet gjorde svært mye nybrottsarbeid innen mange områder for å forbedre tekniske løsninger. Blant annet ble det valgt en ny utforming av betongplattform og dekksanlegg (T-form). Siden rekkevidden for brønnene fra plattformene på Gullfaks ikke dekket hele feltet, ble det planlagt flere havbunnsbrønner i tillegg. Ideen om å bore subseabrønnene før plattformen var ferdigstilt, gjorde at feltet kom tidligere i produksjon enn opprinnelig planlagt. Den første undervannsbrønnen startet produksjonen 22. desember 1986. Ytterligere to brønner ble satt i produksjon før den første plattformbrønnen var klar våren 1987. Det var Kongsberg-gruppen som ble tildelt kontrakten for å produsere de fem undervannsbrønnene (pluss et reservesystem) som skulle kobles opp imot Gullfaks A.
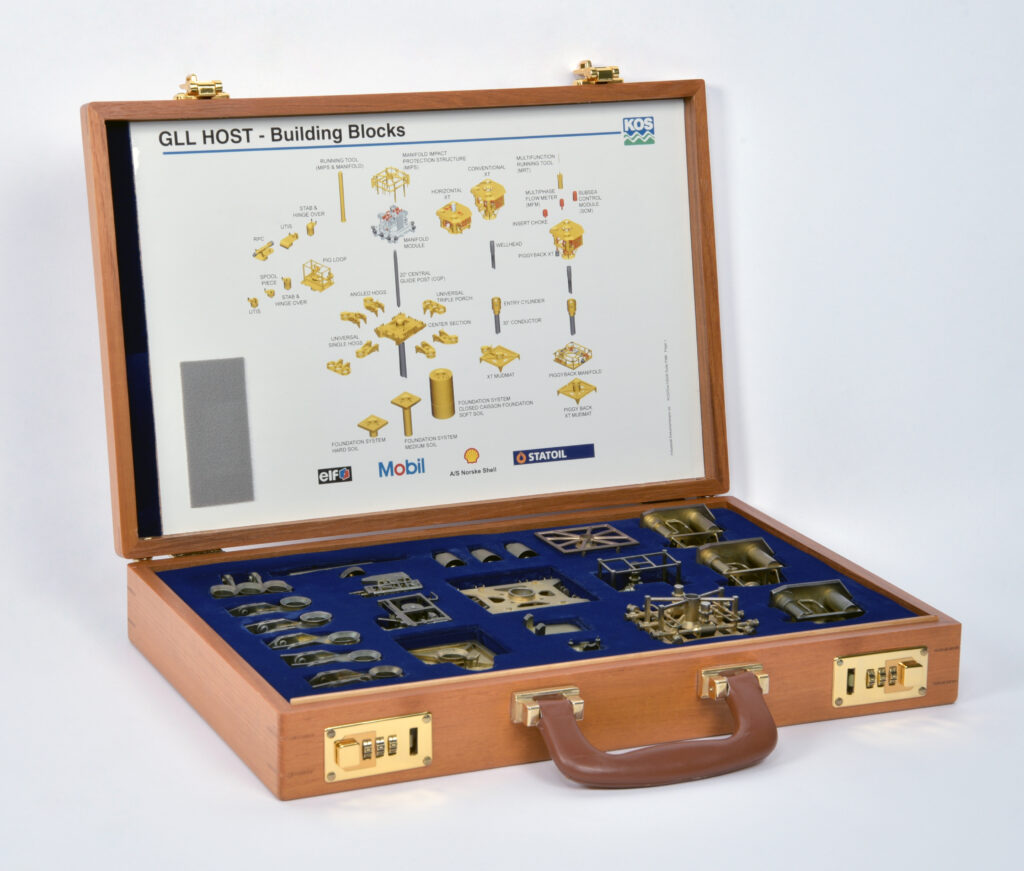
Samarbeidet mellom Statoil og Kongsberg-gruppen hadde startet allerede i 1970-årene. Kongsberg hadde da en samarbeidsavtale med det amerikanske selskapet Cameron for brønnhoder og annet essensielt utstyr. Erfaringene Kongsberg hadde med tidlige studier av Statoils fremtidige utbygging på Tommeliten kom til nytte i Gullfaksutbyggingen. Det samme gjorde forsknings- og utviklingsprosjekter Kongsberg hadde gjennomført sammen med både Elf og Shell for å teste ut undervannsteknologiske løsninger.
Den viktigste nyvinningen på Gullfaks så dagens lys fordi Statoil hadde bestemt seg for at det skulle utvikles løsninger for havbunnsbrønner som kunne installeres og drives uten behov for dykking. Bakgrunnen var at det på dette tidspunktet hadde vært en rekke alvorlige dykkerulykker. Dykking kunne til nøds foregå ned imot 200 meters dyp, men på Norsk Undervannsinstitutt (NUI) i Bergen ble det utført forskningsdykk ned til dybder mellom 400 og 500 meter, med tanke på å ha beredskap for reparasjon av rørledninger som krysset Norskerenna. Statoil bidro økonomisk til denne forskningen.
Siden Gullfaks C (i fase II) skulle plasseres på 215–220 meters dyp og hadde behov for undervannsbrønner, var det ønskelig å utvikle og teste ut dykkerløse systemer. I første omgang skulle dette skje på 140 meter, hvor det tross alt var mulig å gå inn med dykkere hvis det var noe som ikke fungerte. Dermed ble det på Gullfaks A gjennomført nok et nybrottsarbeid ved å installere de første undervannsbrønnene som ikke var avhengig av noen form for dykking. Dette er senere blitt den normale standarden for de fleste undervannsinstallasjonene på norsk sokkel.
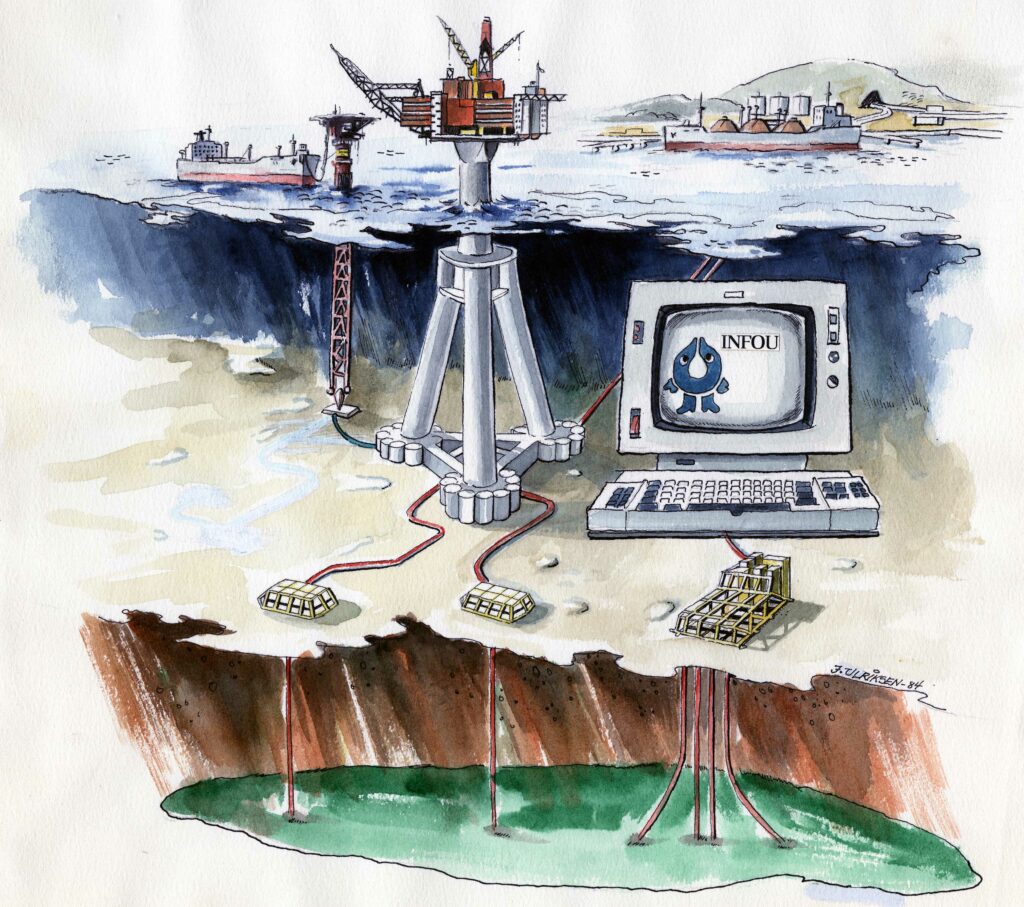
I forbindelse med videreutvikling av betongplattformer ble Statoil svært dyktig på geoteknikk og fundamentering. Gullfaks C og Troll A har ekstremt dype skjørt; dette er betongkappen som omslutter tankene i bunnen av plattformunderstellet. Skjørtene på Troll A er ca. 35 meter. Senere har bøttefundament/sugeanker blitt utviklet basert på denne kunnskapen. Disse brukes både til stålplattformer og til mange undervannskonstruksjoner.
Da oljeprisen sank på midten av 1980-tallet, ble et helt nytt konsept introdusert og tatt i bruk på Veslefrikk. Et understell i stål ble installert for boreplattformen og en halvt nedsenkbar plattform (Semi) med prosessanlegg ble broforbundet med boreplattformen. Dette var den første flytende produksjonsplattformen på norsk sokkel. Erfaringene fra Veslefrikk ble viktig for senere flytende anlegg og ikke minst for videreutviklingen av fleksible slanger.
Andre eksempler på nyvinninger knyttet til Gullfaks er at det var den første plattformen til å ta i bruk stuplivbåter. Et annet fremskritt var at det ble innført enmannslugarer. Senere var Gullfaks det første feltet som kunne slokke gassfaklene på plattformene med en egenutviklet teknologi.
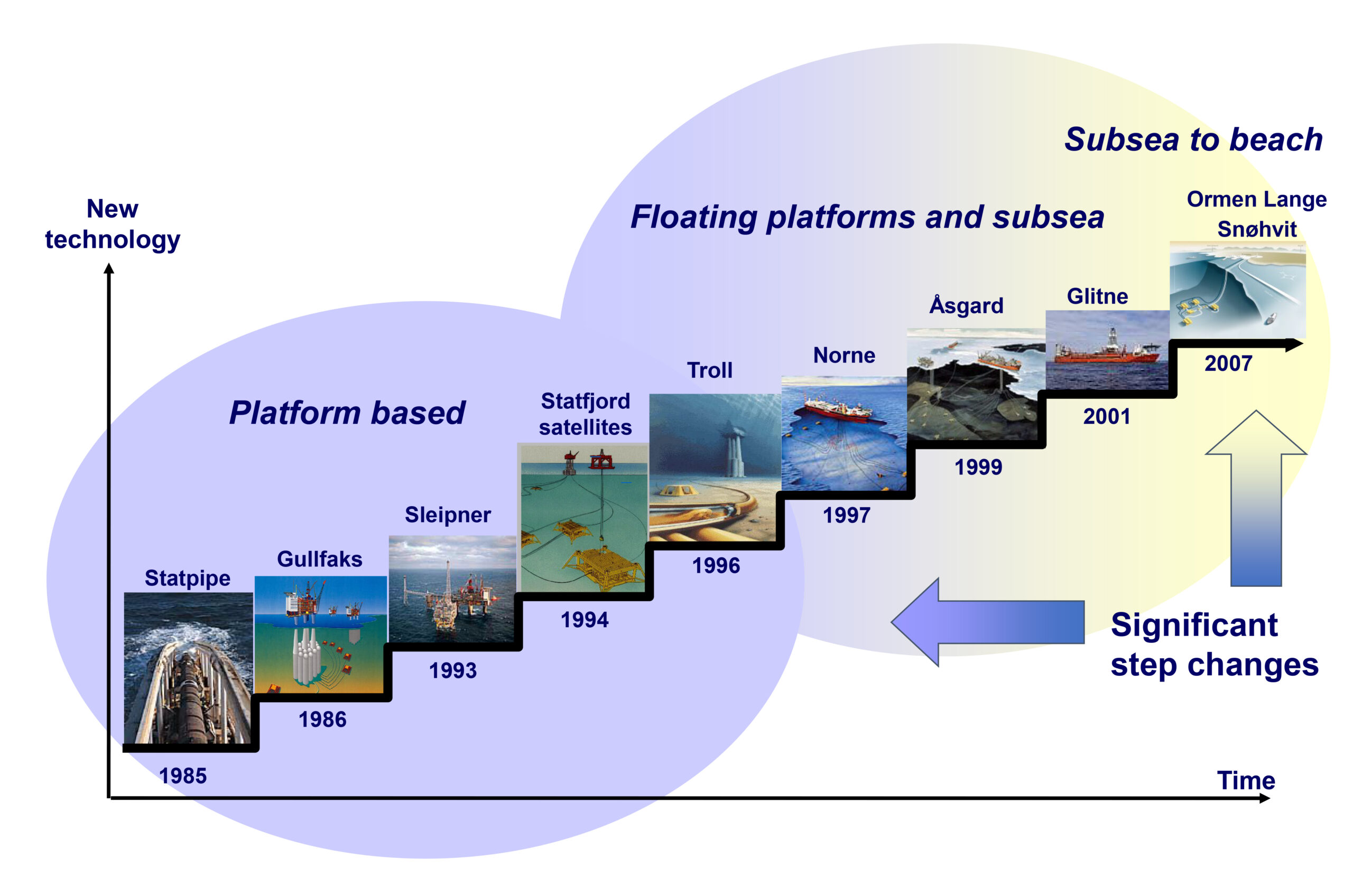
Undervannsløsninger
Iverksetting av nye løsninger i utbyggingsprosjekter krever at det allerede har foregått en utvikling og uttesting av alle del-elementer i teknologien. På slutten av 1970-årene ble det satt større søkelys på å utvikle løsninger hvor oljeselskapene kunne bygge ut feltene, uten å måtte ta i bruk overflateinstallasjoner.
Når det gjaldt Statoil sin utvikling av havbunnsløsninger, ble grunnlaget lagt på Tommeliten og Gullfaks i 1980-årene. Statoils tredje undervannsprosjekt var Statfjord-satellittene. På dette prosjektet igangsatte Statoil sammen med Kongsberg Offshore en systematisk utvikling og standardisering av undervannsteknologi. Disse standardene ble videreutviklet gjennom Norsok-initiativet på 1990-tallet. I dag er disse standardene tatt i bruk globalt og er et viktig fundament for norske undervannsleveranser.
Disse initiativene bidro til at Statoil ble et av de ledende oljeselskapene til å bygge ut og drive felt med et stort antall havbunnsbrønner. Det manifesterte seg på Åsgard, som vi kommer tilbake til senere i denne artikkelen.
For at produksjon fra havbunnsbrønner knyttet til en bunnfast plattform, eller en flytende produksjonsinnretning eller direkte til land skulle fungere, må brønnstrømmen kunne transporteres i rør over en viss avstand uten at det oppstår problemer. Dette måtte det forskes på for å finne gode løsninger.
Statoil var i 1980-årene svært aktive innen forskning på strømning av olje, gass og vann i rør (flerfasestrømning). Forskning og utprøving av løsninger skjedde ved SINTEF sitt anlegg på Tiller i Trondheim. Institutt for energiteknikk (IFE) bidro til å utvikle beregningsverktøyene OLGA og VOLGA. Disse beregningsmodellene ble etter hvert tatt i bruk verden over og har fortsatt en dominerende markedsandel. Det ble videre forsket på hvordan en kan unngå hydratdannelse i rørene. Hydrater dannes når vann og lette hydrokarboner under moderat til høyt trykk kommer i kontakt med hverandre ved temperaturer under 25 grader celsius. Når dette skjer, dannes det is-liknende krystaller, og disse kan tette brønner, rørledninger og prosessutstyr.
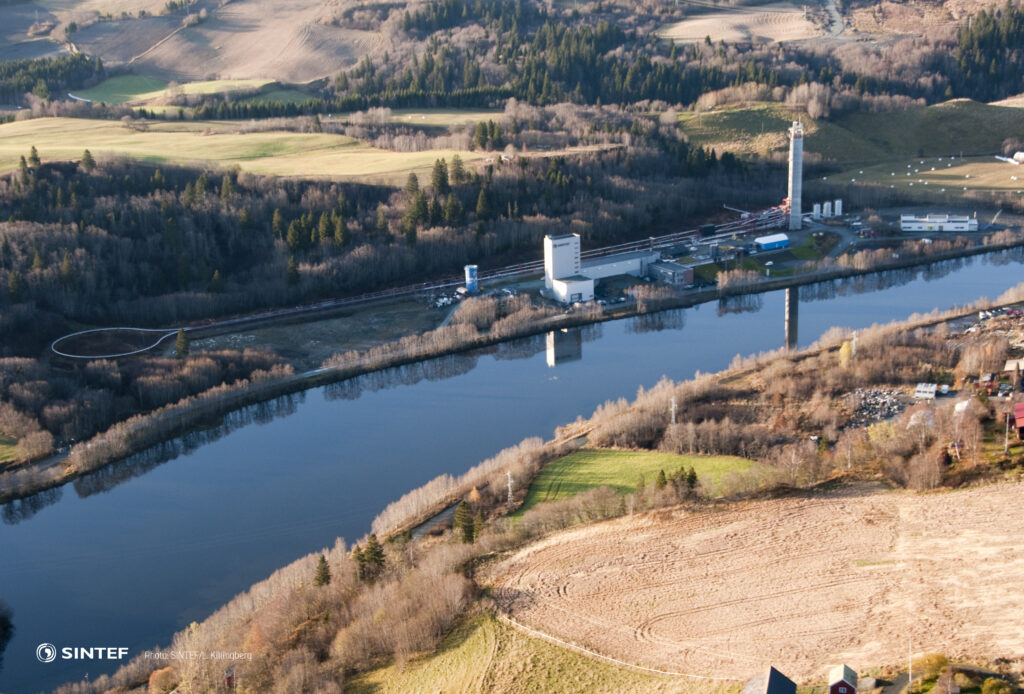
Det at Statoil var langt fremme innen forskning på materialteknologi og flerfasestrømming, fikk avgjørende betydning på utbyggingskonseptet for Troll fase 1. I stedet for å velge å prosessere brønnstrømmen offshore, valgte utbyggingsoperatøren Shell, etter initiativ fra Statoil, flerfasetransport av brønnstrøm direkte til land. Bare vannet blir separert fra brønnstrømmen om bord på plattformen, mens gass og kondensat blir sendt useparert i en flerfaserørledning til gassbehandlingsterminalen på Kollsnes nordvest for Bergen.
På en pressekonferanse i 1989 informerte Norske Shell om at denne løsningen ville kutte utbyggingskostnadene med 4,5 milliarder kroner, og at de årlige driftsutgiftene ville bli 330 millioner kroner lavere. Med 70 års levetid på feltet utgjør dette store beløp.
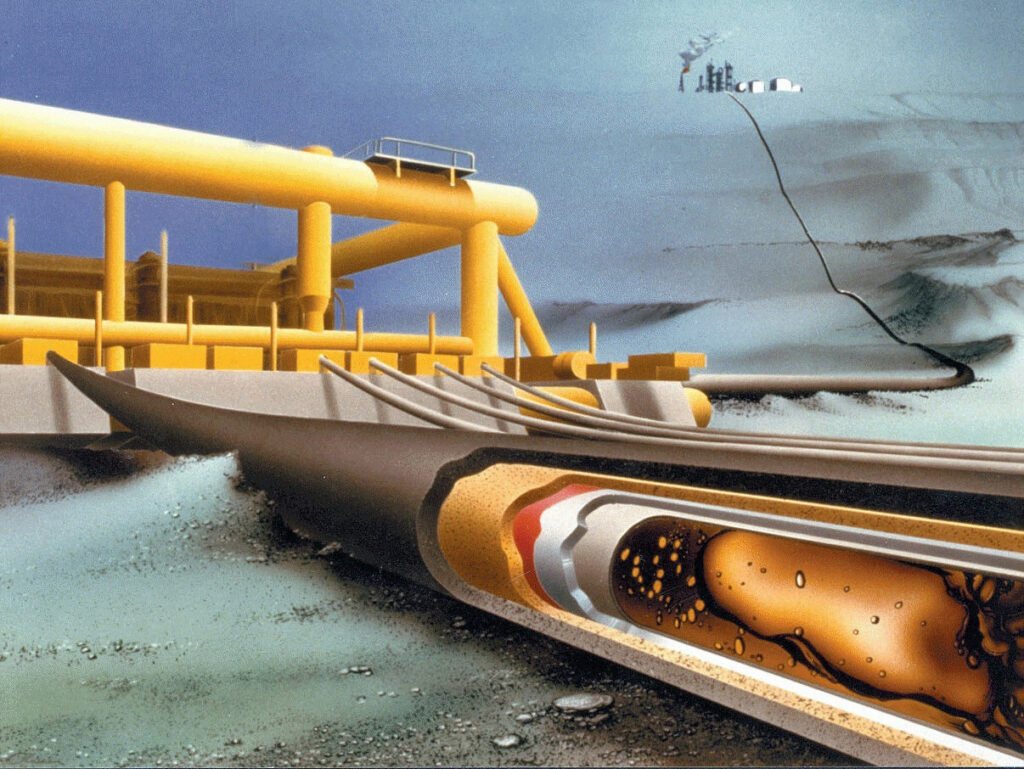
De første flerfaserørledningene ble lagt på slutten av 1980-tallet. De avgjørende gjennombruddene for flerfaseteknologien kom med Hydros Troll-Oseberg Gassinjeksjon (TOGI)-prosjekt og med utbyggingsløsningen på Troll A. Disse prosjektene viste at flerfasetransport kunne gi store besparelser ved utbygging, samt gjøre marginale felt lønnsomme. Utbyggingskostnadene for felt som tidligere ikke hadde vært økonomisk forsvarlige å bygge ut, kunne nå reduseres og settes i produksjon med en undervannsløsning tilkoblet et prosessanlegg på land, eller til en nærliggende plattform med kapasitet.
Flerfaseteknologi: Transport av olje, gass og vann i samme rørledning over stadig lengre avstander. Kan gjøre felt mer lønnsomme og gjøre utbygginger i værharde strøk og på dypt vann mulig.
To eksempler på rene undervannsløsninger uten noen plattform eller noe produksjonsskip er gassfeltene Snøhvit og Ormen Lange, som begge ble satt i drift i 2007. Ingen av disse «subsea to shore»-prosjektene ville blitt bygget ut på denne måten uten resultatene fra flerfaseforskningen.
Flytende plattformer på større dyp
I løpet av åttitallet ble det gjort mange funn på Haltenbanken i Norskehavet. Vanndybden her er fra 300 meter og nedover. Bunnfaste plattformer ble da dyre. Det eneste eksempelet på en bunnfast plattform nord for Stadt er Draugen.
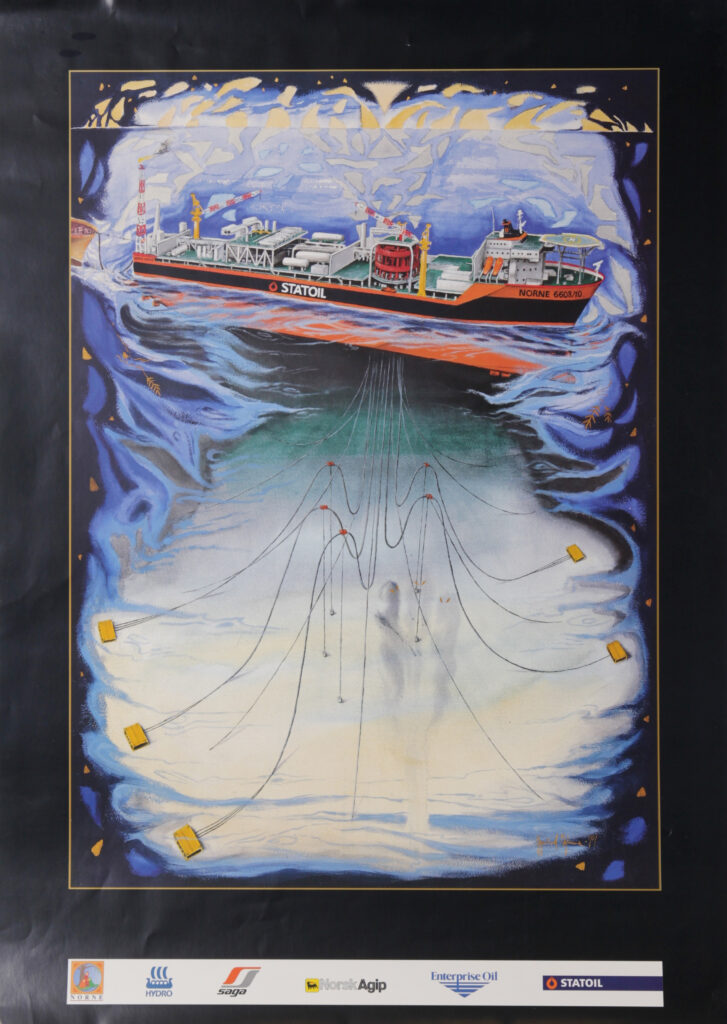
Alternativet til bunnfaste plattformer var flytende installasjoner. Dette var nybrottsarbeid. Heidrun ble vedtatt i 1991 basert på en løsning med en strekkstagsplattform og en egen gassløsning med ilandføring til Tjeldbergodden, hvor det ble bygget en metanolfabrikk. De neste prosjektene var Statoils Smørbukk og Smørbukk Sør, Hydros Njord og Sagas Midgard. Både Njord og Smørbukk Sør kunne klare seg uten en gasseksportløsning i en del år ved å reinjisere gassen, mens Smørbukk og Midgard var helt avhengige av å få transportert gassen sørover. Både Saga og Statoil, som var operatører for hver sine gassfelter, fant det vanskelig å lage lønnsomme utbyggingsløsninger.
Det var ikke bare økonomien det sto på. Det gjaldt også å finne teknisk gjennomførbare løsninger for de flytende produksjonsinnretningene. Kapasitetsbehovet for installasjonene på Haltenbanken var vesentlig større enn det som hadde vært vanlig for flytende produksjonsinnretninger. I tillegg kom høyere trykk og temperatur på brønnstrømmen og større bevegelser i anlegget på grunn av vind og bølgehøyder. Smørbukk Sør-lisensen hadde sin utbyggingsplan klar i 1992, men valgte først å kvalitetssikre teknologien som gjør at skipet kan dreie rundt med vinden (svivel/turret) uten at produksjonen stopper. På et produksjonsskip kommer de fleksible rørene opp gjennom en dreibar sylinder midt i skipet som tar opp skipets rotasjon i forhold til sjøbunnen og derved tillater at skipet kan snu etter været.
Dette ga Norne-prosjektet en «kickstart» året etterpå. Norne-løsningen for produksjonsskip ble en tilnærmet kopi av det konseptet som var utredet av Smørbukk Sør. Norne var Statoils første utbygging basert på en flytende skipsformet plattform knyttet til undervannsbrønner med fleksible stigerør. Norne ble et vellykket prosjekt både med hensyn til gjennomføringstid, kostnader og kvalitet. Det ble også et foregangsprosjekt for nye måter å samarbeide med leverandørindustrien på.
Fleksible stigerør: Bøyelige rør som går fra havbunnen til en flytende produksjonsenhet. Ettersom «flytere» beveger med bølger og vind, må rørene være fleksible.
I 1994 ble rettighetene til Smørbukk, Smørbukk Sør og Midgard samordnet i en ny eierstruktur med Statoil som operatør. Prosjektet fikk navnet Åsgard og er blant de største utbyggingene på norsk sokkel noensinne, med sine 63 produksjons- og injeksjonsbrønner fordelt på 19 brønnrammer på havbunnen. Antall undervannsbrønner var det største i verden til da.
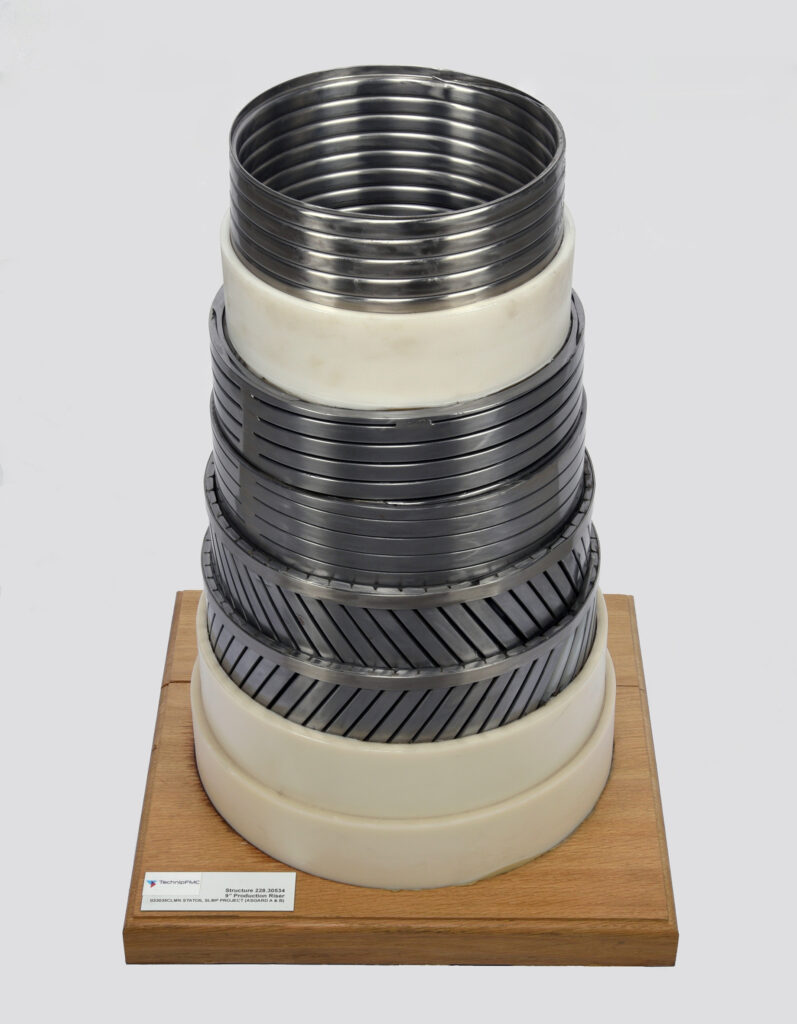
Prosjektet utvinner gass, kondensat og olje fra tre svært forskjellige og krevende reservoarer. Åsgard A var verdens til da største FPSO (Floating Production, Storage and Offloading) og Åsgard B var den første flytende gassprosesseringsplattformen med en kapasitet på denne størrelsen. Mer enn 20 omfattende teknologiutviklingsprogram foregikk parallelt med prosjektet. Disse omfattet fjerning av hydrogensulfid, bundler (inkludering av ulike typer rør og signalkabler i en streng), «pig launcher» (stasjon for å sende rørskraper tilbake til plattformen), svivel/turret, flerfasemålere, fleksible stigerør med mer.
Åsgard har i hele sin levetid fungert som et kjempelaboratorium for å komme opp med nye ideer, utvikle disse for deretter å ta dem i bruk – for eksempel innen subsea-kompresjon. Statoils eget teknologimiljø, industripartnere og underleverandører har igjennom Åsgard-prosjektene utviklet og tatt i bruk ny teknologi i verdensklasse.
Et annet eksempel på teknologiutvikling under vann var separasjon og vanninjeksjon på Tordis.
Betydning for Statoil/Equinor
Teknologiutviklingen som Statoil var en del av på norsk sokkel har vært til stor nytte når selskapet har etablert seg i andre land med oljeproduksjon til havs.
I Mexicogolfen og på brasiliansk sokkel beveget operatørene seg gradvis ut på enda dypere vann enn det som ble gjort i Norge. Dette, sammen med teknologiutviklingen på norsk sokkel, ble avgjørende for de store utbyggingene i Angola og Nigeria som startet opp rundt årtusenskiftet. Statoil var da, takket være sin teknologiinnsats på norsk sokkel, en velkommen aktør i nye dypvannsområder, både som deltager i og operatør for krevende utbygginger.
Basisen for det som i ettertid kan kalles en bragd, var en bevisst strategi rundt utvikling av ny teknologi, en sterk vilje og ikke minst mot til å inkludere nye løsninger i egne prosjekter i tett samarbeid med leverandørindustrien. Dette ga selskapet en konkurransefordel og et godt renommé.
For den norske delen av industrien har Statoil/Equinors vilje til både å dele nye tekniske løsninger og samtidig stimulere og hjelpe leverandørene med å utvikle nye smarte løsninger vært avgjørende for den konkurransekraften norsk industri har bygget opp globalt de siste 20–25 årene. I dag er leveranser av tekniske løsninger og tjenester til den globale oljeindustrien Norges nest største eksportnæring, etter salg av olje og gass. Dette har gitt en enorm verdiskapning for eierne og for det norske samfunnet.
Equinor ønsker nå å fortsette som et ledende energi- og industriselskap inn i det «grønne skiftet». Da kan det være lurt å trekke lærdom av suksessoppskriften for blant annet teknologiutvikling som i første omgang gjorde det til et verdensledende selskap innen olje og gass.
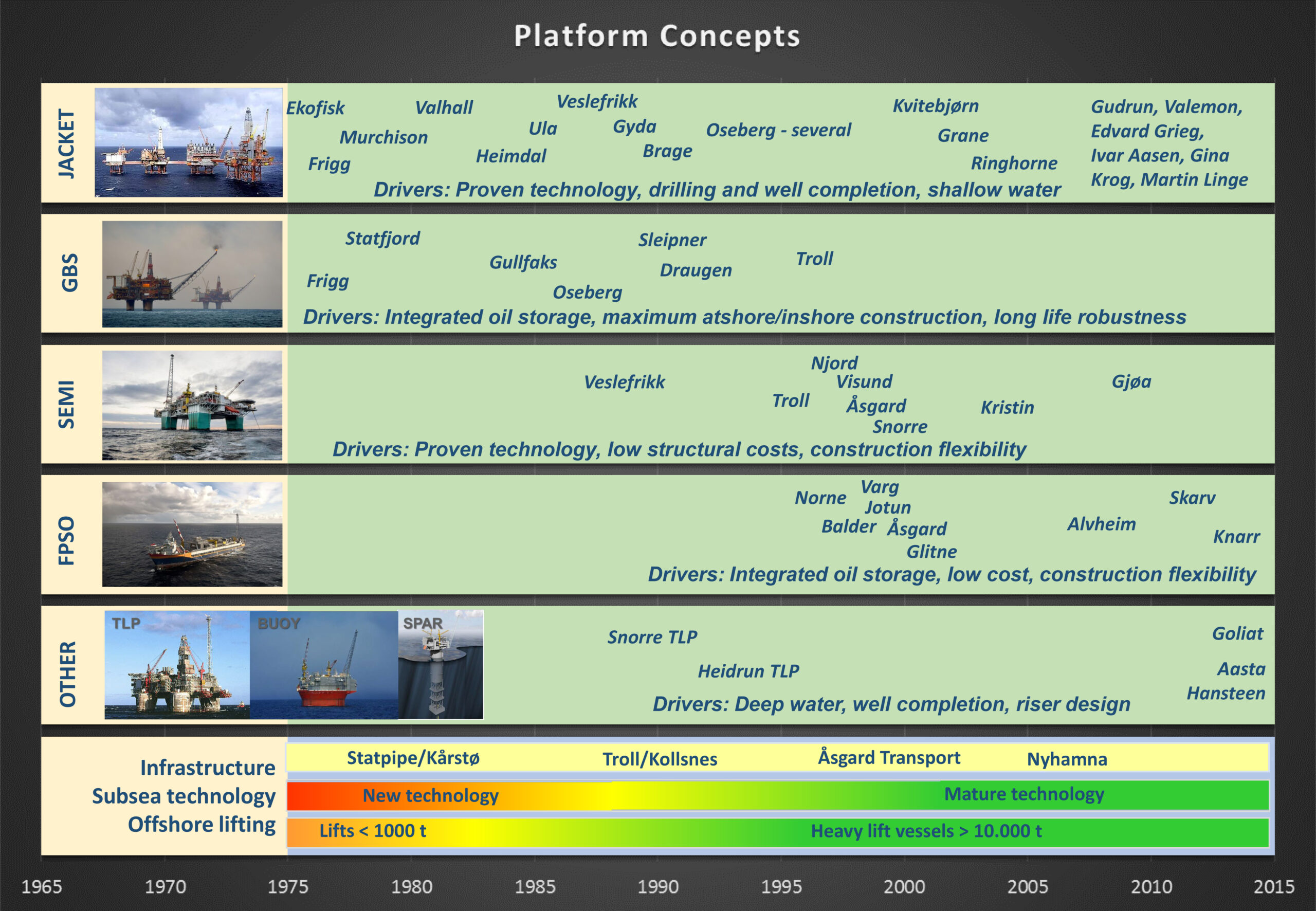