Bolts from the blue

Sleipner East and the Loke satellite were due to start production on 1 October 1993 with the first deliveries under the big Troll gas sales agreement – the world’s biggest energy contract to date. Bringing Sleipner on stream had proved a lengthy and difficult journey – not least with the loss of the concrete gravity base structure for Sleipner A in the Gands Fjord off Stavanger in 1991. That had forced operator Statoil to think afresh. One consequence of this setback was that the first production wells would not be drilled from the A platform, but as subsea completions installed in seabed templates. And one way to save time here was to “hijack” structures already under construction.
Originally intended for water injection on Statfjord North and East, these were diverted to Sleipner and Loke. Wells could then been predrilled and three of the four Xmas trees put in place. These units are assemblies of valves intended to regulate the wellstream from the reservoir, and represent an important safety barrier in preventing an uncontrolled escape of hydrocarbons.
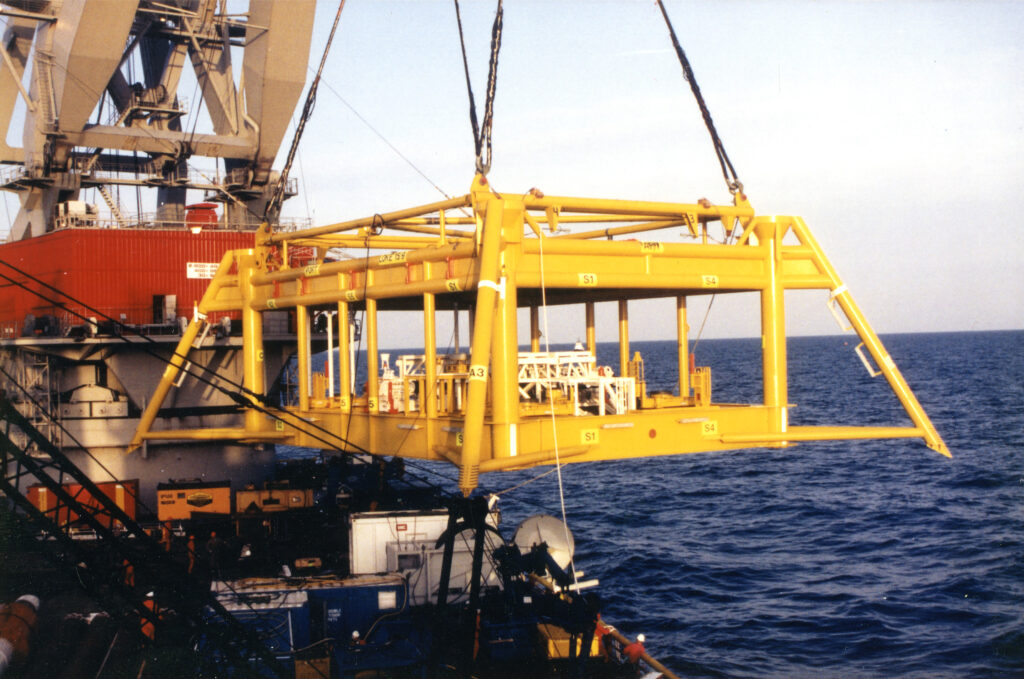
Drama in Dusavik
The alarm sounded at the Dusavik base outside Stavanger mere months before production was due to begin. Damaged bolts attaching the main valves were found on the fourth tree, which was waiting to be shipped to field. Since these bolts had a critical function, the big question now was the condition of almost 100 of them installed on the three trees already in place.
Would it now be necessary to plug all the pre-drilled wells, retrieve the trees and inspect their bolts in order to make sure production could safely start? Doing so would be hugely expensive. It would also delay the start of deliveries under the Troll agreements, which put considerable prestige at stake. Was Statoil willing to take a chance that the installed bolts were good enough, with the threat of a blowout if they proved inadequate?
Or could another solution be found?
Mobilising expertise
For several reasons, using divers to investigate the bolts was not an option. One consideration was safety – messing with the equipment could unleash a full gas blowout when people were nearby, and cause possible fatalities. Another concern was accuracy and repeatability. A diver was unable to hold the sensor with sufficient stability, so a form of mechanical device would have to be developed regardless. That made it reasonable to think of remotely operated vehicles (ROVs).
Hans Jørgen Lindland, Statoil’s chief engineer for subsea technology, had no solution to the problem himself but knew where to go to find one. Rolf Saltkjel was a senior engineer for subsea technology, whose experience included the use of ultrasonics, ROVs and non-destructive testing (NDT). That was a good combination for tackling the present problem.
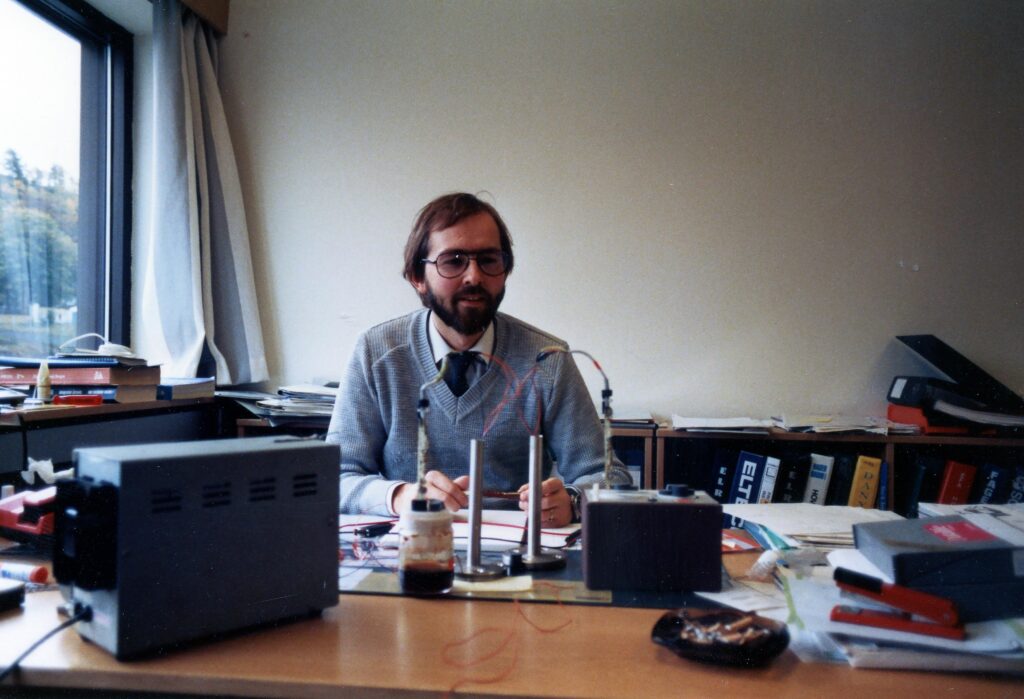
There was no time for preliminary studies, project descriptions or decision gates. People just had to get down to it. Both Statoil’s corporate executive management and the Norwegian Petroleum Directorate (NPD) were contacted, informed of the problem and told a proposed solution would soon be submitted.
“It became long days and many hours in the garage,” Saltkjel recalls. “We faced a number of challenges – finding an ROV small enough to reach the bolts, creating an inspection system which offered sufficient confidence in the results, and installing this on the vehicle.”[REMOVE]Fotnote: Interview with Rolf Saltkjel and Hans Jørgen Lindland, 17 December 2021.
The answer was not to build something new, but to combine known technology in an innovative way. A tailormade crescent-shaped “cup” which could grip tight to each nut was attached to the ROV, using a dynamic arm to absorb vehicle movements. This part of the solution was actually patented afterwards. It was supplemented with a focused ultrasonic beam to investigate each bolt for cracks, which took about four minutes at a time.
Statoil’s top management had faith in the organisation’s ability to find solutions, but was undoubtedly surprised when it was presented with this contraption – which looked like something by Heath Robinson (or Rube Goldberg, as Americans would say). Part of the modification for transferring power from the ROV to the inspection unit depended on a “flexible drive mechanism”. In response to a direct question, Saltkjel admitted that this was the speedometer wire from a moped. All the same, it worked perfectly.
To verify, this newly developed method, bolts of the same type as the ones on the trees were located – some with and some without cracking. During a blind test, where those operating the instruments did not know which of the bolts were damaged, both the equipment and the operators functioned well enough to identify the defective units. That was sufficiently convincing for the trials to be moved offshore for full-scale investigations.
Saltkjel and his colleagues set off for Sleipner with the newly developed ROV system and started investigating the bolts. Not all of these were accessible, even though the ROV was one of the smaller models. But it proved possible to investigate enough of them to be convinced that the results were representative. No faults were found on any of the bolts.
Both the method and the findings were sufficient for Statoil’s top management and the NPD. An application was eventually made for consent to start up, and the first well from the Sleipner D facility came on stream on 24 August 1993 – in good time before deliveries to continental Europe were due to begin.
Problem identified
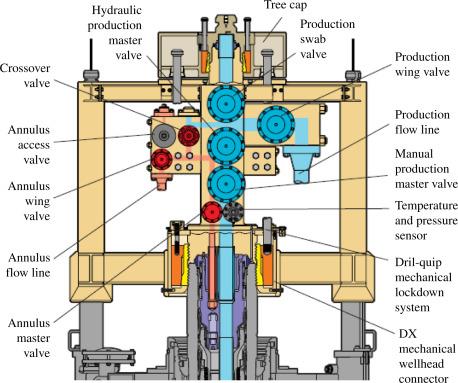
So what about the fourth tree and its damaged bolts? According to Saltkjel: “We never fully identified why they failed, despite a thorough investigation.
“It could have been down to a different production method for these bolts, and the way they were cooled down after being cast. Even though we never found a ‘smoking gun’, however, we were satisfied that the installed bolts would last.[REMOVE]Fotnote: Interview with Rolf Saltkjel and Hans Jørgen Lindland, 17 December 2021.
Similar problems could hardly have been overcome in the same way today, Lindland admits. Governing documentation and applicable regulations would undoubtedly have called for the wells to be plugged immediately. But confirmation that the solution chosen back in 1993 was viable can be found today on the seabed in 85 metres of water on Sleipner.
arrow_backGas from Sleipner East to EuropeFuelling the Olympic flamearrow_forward