CCS on Sleipner – back where it came from

Sleipner West was discovered as early as 1974 with Esso as the operator and declared commercial in 1984. After a plan for development and operation (PDO) was submitted to the government in 1992, it came on stream in 1996. But something had to be done about the high CO2 content in the field’s output in order to meet the specifications in the gas sales contract.
While natural gas primarily comprises methane (CH4), it also contains varying amounts of undesirable substances such as hydrogen sulphide (H2S), nitrogen and carbon dioxide (CO2). Many fire extinguishers contain pure CO2 because it displaces the oxygen needed to sustain combustion. This is also why a high CO2 content is undesirable in natural gas for use with ovens and the like – it will not burn so well. As a result, gas sales contracts will often specify a maximum quantity of undesirable substances permitted on delivery in order to ensure combustion quality.
Scrubbed clean and stored
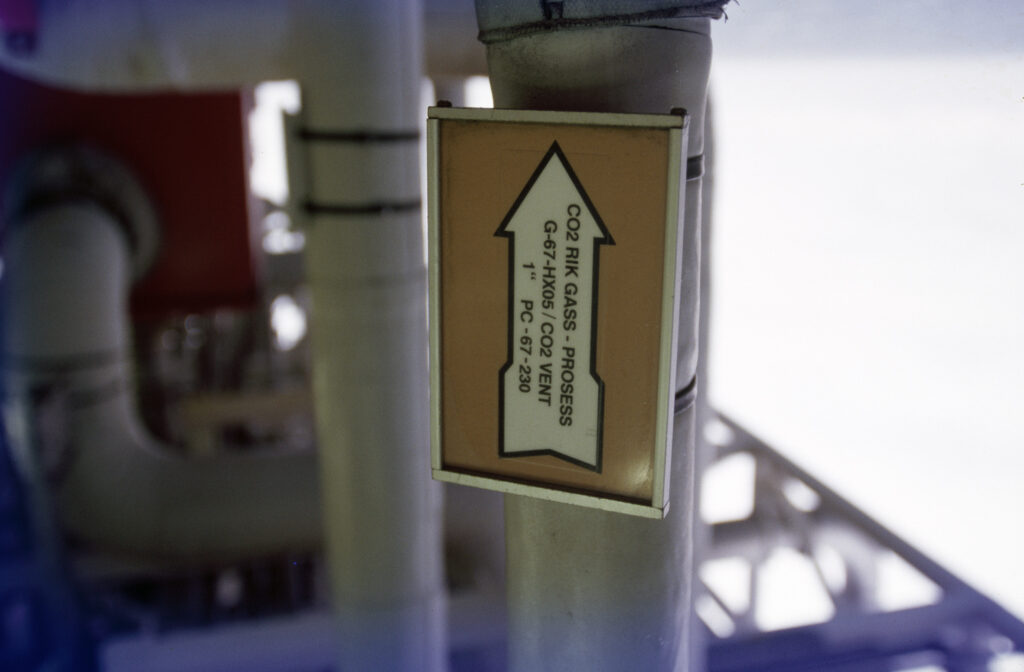
The gas in Sleipner West comes from 3 450 metres beneath the seabed and contains about nine per cent CO2. That exceeds the ceiling specified in the Troll gas sales agreements, which is 2.5 per cent for this component. As a result, the excess CO2 must be removed before exporting the gas. This is done in two ways – by blending the Sleipner West gas with gas from Sleipner East and other fields with low CO2 content. To further reduce the CO2 content in the exported Sleipner West gas, CO2 is removed from it. This is done by adding amines – organic bases containing a nitrogen atom which bind to the CO2 – on the separate Sleipner T gas treatment platform tied back to the concrete Sleipner A installation.
After being removed from the gas flow, the CO2-rich amines are heated to separate the mix into its component parts again – a process called scrubbing. That allows the amine to be reused and leaves the CO2 to be disposed of. This technology was not off-the-shelf, and had some problems and was costly. Countless modifications had to be made. One favorable factor for Statoil as operator was that the technology used was from the French company Total. Total was also a partner in the license, and hence did not cause much commotion when there was trouble with the technology. [REMOVE]Fotnote: Kyrre Nese in e-mail 8. august 2022.
CO2 is re-injected
Since the latter has no commercial value, the simplest – and cheapest – way of dealing with this gas would be to release it to the air. That might have been done on Sleipner West, too, but the introduction of a Norwegian carbon tax for petroleum operations on the NCS meant it would be very expensive. So operator Statoil opted for a different approach, which involved pumping the CO2 back underground. Since returning the gas to the reservoir of origin would simply increase its content in future production, the geologists had to find somewhere else to put it.
A number of conditions must be in place for CO2 to be stored in the sub-surface. The relevant formation must have sufficiently porous and permeable rocks, be saturated with saline water, be deep enough (more than 800 metres below sea level) to ensure that the CO2 has the desired properties, have an impermeable cap rock to prevent the gas leaking out, and cover a sufficiently large area with a big enough volume.[REMOVE]Fotnote: https://bellona.org/assets/sites/3/Case_Study_on_the_Sleipner_Gas_Field_in_Norway.pdf
The Utsira formation, which overlaps the Sleipner reservoirs at a different depth, meets these criteria and represents an ideal location for disposing of CO2. It lies about 800 metres beneath the seabed, while the main Sleipner East reservoir is roughly 1 700 metres further down.
Using a single well drilled from the concrete Sleipner A platform, an annual injection rate of about a million tonnes means some 20 million tonnes of CO2 have been deposited in the Utsira formation since 1996.
Regular investigations of the sub-surface have been conducted using seismic surveying to ensure that no CO2 is leaking from the structure to the seabed. These studies show that the injected gas is occupying an ever-expanding area of the formation and that no threat of leaks exists.
CO2 injection from Sleipner West was a pioneering project on the NCS and has been a success. Since 2019, CO2 from Utgard – which comprises no less than 16 per cent of this field’s output – has also been separated out on Sleipner T and injected into the Utsira formation.[REMOVE]Fotnote: Annual report Utgard 2019, AU-UTG-00002, Equinor.
The Snøhvit gas produced in Norway’s Barents Sea sector contains five-eight per cent CO2. This is separated out in the same way as on Sleipner, but at the Melkøya processing plant on land rather than on an offshore platform. Separated CO2 is piped back to the field in a compressed liquid phase and injected into the subsurface. Although injection problems have arisen, studies indicate that no gas is leaking out. A similar CCS process was pursued on the Salah gas field in Algeria, but terminated in 2011 because of capacity limitations in the geological structures.[REMOVE]Fotnote: https://uit.no/om/enhet/aktuelt/nyhet?p_document_id=552337&p_dimension_id=88137 and https://www.equinor.com/energy/carbon-capture-utilisation-and-storage
CCS on Sleipner has been under way longer than any comparable project, and the data and experience this has yielded will be important for future schemes of this kind. In 2019, Equinor and its partners in the field released information on CO2 injection and monitoring as a contribution to innovation for and development of storing greenhouse gases.[REMOVE]Fotnote: https://www.equinor.com/news/archive/2019-06-12-sleipner-co2-storage-data