In the driving seat for subsea compression

The world’s two first seabed compression units became operational in the autumn of 2015, with the bigger – Åsgard subsea compression – starting up on 16 September and Gullfaks wet gas compression following a month later.[REMOVE]Fotnote: This article builds to a great extent on Gjerde, Kristin Øye and Nergaard, Arnfinn, 2019, Getting down to it. 50 years of subsea success in Norway: 247-250.
Separation and compression
Production from a seabed well emerges as a mix of oil, gas, water and sand from the reservoir, known as the wellstream. This flow is separated into its various components – in some cases on the seabed. Since water and sand are superfluous, they are removed and injected back below ground. Oil and gas emerging from the separator are piped away separately.
When a reservoir has been on stream for a while, pressure in the wells declines and the production pace gradually slows. To combat this, pumps can be used to speed up the oil flow. Where gas is concerned, installing a compressor will raise its pressure and increase transport speed. These devices can also be positioned subsea.
The reason for moving separators, pumps and compressor to the seabed in this way is that they are large and heavy devices. Removing them from platforms saves both space and weight.[REMOVE]Fotnote: Exhibition on subsea working, Norwegian Petroleum Museum, 2021.
Åsgard subsea compression 2015
The first person to come up with the idea of subsea compression was Norwegian Kjell Olav Stinessen, who produced a simple drawing to illustrate the concept in 1985. Thirty years later, his vision was realised when the first installation of this kind was placed on the Åsgard field in the Norwegian Sea.
Developed by Statoil in cooperation with Aker Solutions and ABB, this station is as big as a football pitch – 73 by 44 by 23 metres – and weighs 5 100 tonnes.
One reason such a large facility has been required on Åsgard is because it was discovered after output started in 1999 that the Midgard and Mikkel satellite fields might have a limited producing life. Pressure conditions and the ratio between gas and condensate were problematic and could lead to an early shutdown.[REMOVE]Fotnote: Gjerde, Kristin Øye and Nergaard, Arnfinn, op.cit: 247-248.

Ways to avoid this were available. Statoil calculated that a compressor station of a certain size would improve gas and condensate recovery from these satellites by 300 million barrels of oil equivalent (boe).
Another reason for installing the facility was that production from Midgard and Mikkel helped to balance the quality of Åsgard’s gas, where CO2 exceeded the level specified in the sales contract. Adding Midgard/Mikkel output, where the carbon content was much lower, yielded a better mix.[REMOVE]Fotnote: Bøe, Arnt Even “God på bunnen» Norsk sokkel/Kvantesprang, Norwegian Petroleum Directorate, 19 December 2016; Norsk Petroleum, Mikkel.
Statoil awarded a contract for a subsea facility to Aker Solutions in October 2010, with construction at the latter’s yard in Egersund south of Stavanger. The delivery comprised a big compressor station, a new manifold station, an extensive system of new pipes and connections, and a high-voltage power module on Åsgard A.[REMOVE]Fotnote: Time, N P and Torpe, H, 2016, “Subsea Compression- Åsgard Subsea Compression, Start-Up and Operational Experience” OTC-27163-MS.
In principle, the process for Åsgard compression is straightforward. Condensate and gas first pass through a separator. The gas pressure is then raised while controlling the process temperature, and condensate gets pumped up to the same pressure level as the gas. The two components are then remixed, and emerge from the compressor at a higher pressure and speed.
As an indication of the forces involved, each compressor is driven by an electric motor with a shaft power of 11.5 megawatts. That corresponds to more than 30 000 horsepower, comparable with the output of a Boeing 737-500 engine.
Åsgard compression was expected to improve recovery factors from 67 to 87 per cent for Midgard and from 59 to 84 per cent for Mikkel. That adds up to 306 million boe.
After a year, Halvor Engebretsen, operations vice president for Åsgard, could report that an additional 16 million boe worth NOK 5 billion had been produced.[REMOVE]Fotnote: Petro.no, “Åsgard – Økt utvinning verdt 5 milliarder”, 1 October 2016.
This did not go unremarked. In August 2016, the Norwegian Petroleum Directorate (NPD) awarded its improved oil recovery (IOR) prize to the Åsgard licensees – Statoil, Petoro, Total, Eni and ExxonMobil. Making the presentation, NPD director general Bente Nyland said:[REMOVE]Fotnote: “IOR prize award to Åsgard licensees”, general news, Norwegian Petroleum Directorate, 30 August 2016.
[This] naturally involves risk, and we therefore acclaim technology development and pilot projects. When we see that these succeed, as has been the case with Åsgard, we must recognise the inventiveness and boldness displayed by the companies. They have taken an investment risk, and can now reap the reward.”
Åsgard subsea Gas Compression, av Equinor
Gullfaks subsea compression 2015
Framo Engineering was also interested in compressors. This Bergen-based company – which changed its name to OneSubsea in 2013 – was noted in the 1980s and 1990s for its oil-industry pumps. These ranged from simple units to advanced multiphase products.
With support from the government-funded Demo 2000 research programme, Framo participated in a project to develop a large wet gas compressor. It secured a contract from Statoil in May 2009 to develop such a device. As with Åsgard, the aim was to improve recovery. Placing two compressors in parallel in the wellstreams from two seabed templates was expected to improve recovery by 22 million boe and thereby raise the recovery factor from 62 to 72 per cent.[REMOVE]Fotnote: Teknisk Ukeblad, “Much to be gained from subsea processing”, 15 August 2002.
The wet gas compressors built by Framo for Gullfaks represented a further advance in terms of motors, seal systems and bearings.[REMOVE]Fotnote: Wadel-Andersen, Fredrik, WGC system for Statoil Gullfaks, Framo PDF presentation. They were smaller than the Åsgard compressors, with just under half the output. Flow volumes were also roughly half the capacity on the other field. Each compressor was driven by two motors.
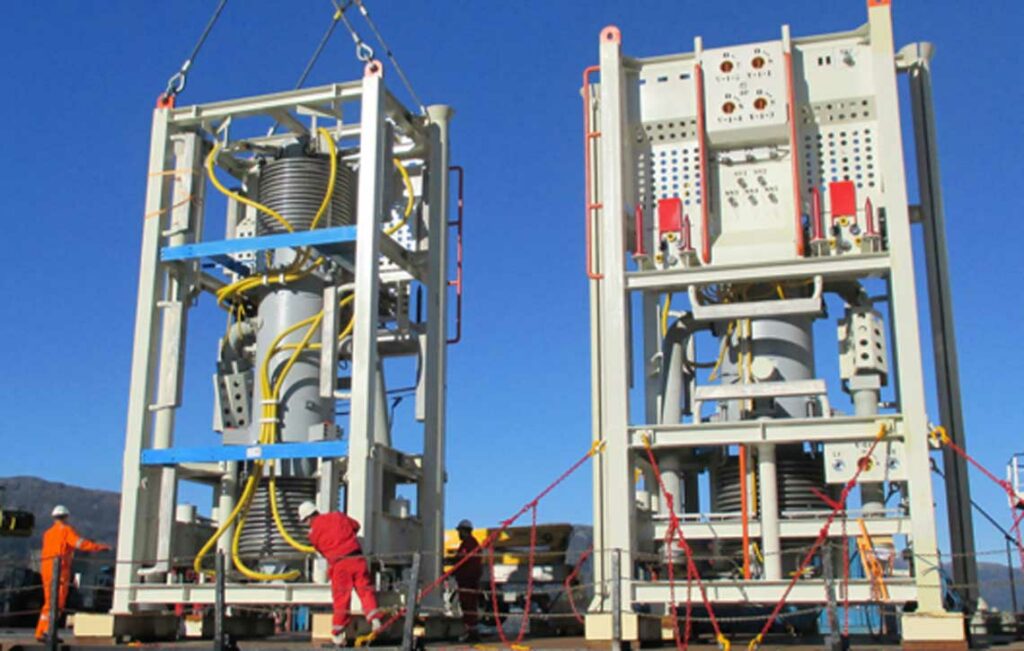
A contract to produce the whole system was awarded in May 2012, about 18 months after the corresponding job for Åsgard was given to Aker Solutions. The Gullfaks compressor station is a compact structure weighing just over 1 000 tonnes in all and measuring 34 by 19 by 12 metres.
Gullfaks compression had a troubled start-up. The decision was taken in May 2016 to retrieve both compressors for a check-up. That followed a leak in the 16-kilometre umbilical from Gullfaks C. It took two years to put a new umbilical in place, with the station coming back on line in June 2017 and working as intended thereafter.[REMOVE]Fotnote: Jon Arve Sværen in a phone conversation with Arnfinn Nergaard, 8 June 2018.
Despite the running-in problems with the wet gas compressors, both of the Norwegian gas compressor projects can be considered technological triumphs in subsea history. Whether they become commercial successes beyond whatever the pioneer developments might achieve remains to be seen.
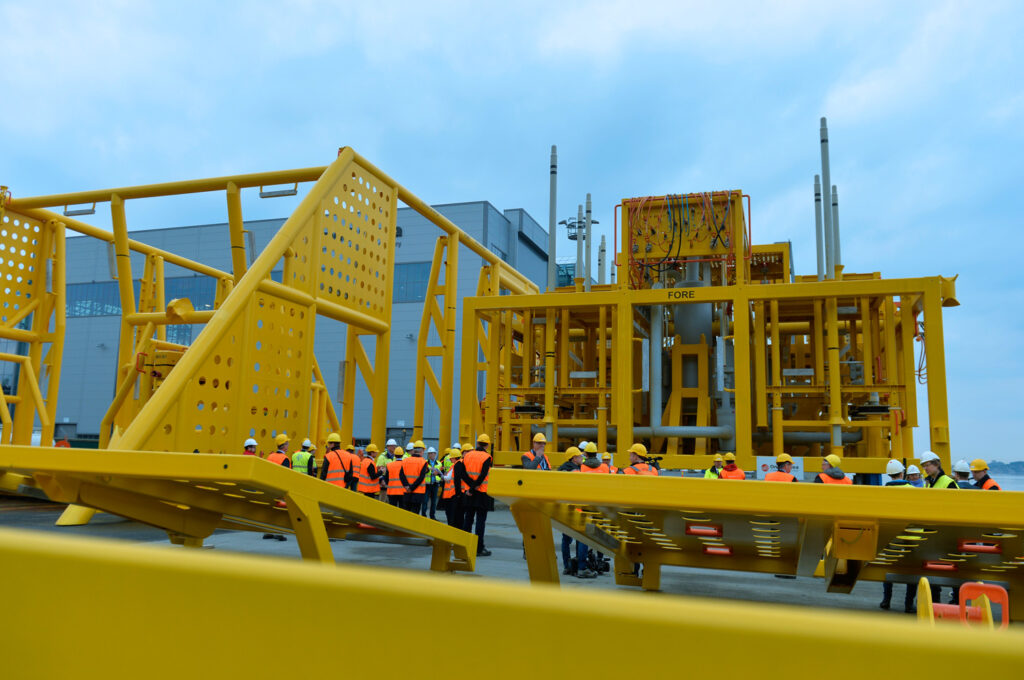