Seabed separator

Subsea processing can be defined as any active treatment of the wellstream – a mix of oil, gas, water and sand – on the seabed. That may involve pumping, separation and processing, water injection or gas compression.
Benefits of reusing water
The water and sand which accompany oil and gas up from a well represent a problem which needs to be eliminated. A goal in several technology development projects has therefore been to find ways of removing the water as soon as possible.
Ingenious engineers have found that separating water out on the seabed, as close to the wellhead as possible, offers several benefits. First, the remaining wellstream will then rise more easily to the platform and thereby increase production. Second, injecting the separated water into a nearby formation could help to maintain reservoir pressure – with the potential to improve recovery. Third, no separation plant will be needed on the platform, reducing this topside weight and thereby cutting design and construction costs.[REMOVE]Fotnote: Exhibition on subsea working, Norwegian Petroleum Museum, 2021.
Two Norwegian projects by different companies have realised solutions for subsea water injection facilities. The first was Troll Pilot, pursued by Norsk Hydro and ABB in 2000. That was followed by the Tordis improved oil recovery (IOR) project involving Statoil and FMC Technologies in 2007, which will be covered in more detail below.
Separation and water injection on Tordis
The forerunner to Tordis IOC was an FMC Technologies project which received support in 2001 from Norway’s Demo 2000 programme.[REMOVE]Fotnote: The negative consequences of the 1998–99 oil crisis prompted the Norwegian government to appropriate funds for the Demo 2000 research programme, which kicked off in 1999. Throughout the 1990s, Statoil had collaborated closely with supplier Kongsberg Offshore. Renamed FMC Technologies, the latter used the Demo 2000 funding to develop a subsea separator able to handle continuous sand throughput, similar to Troll Pilot.
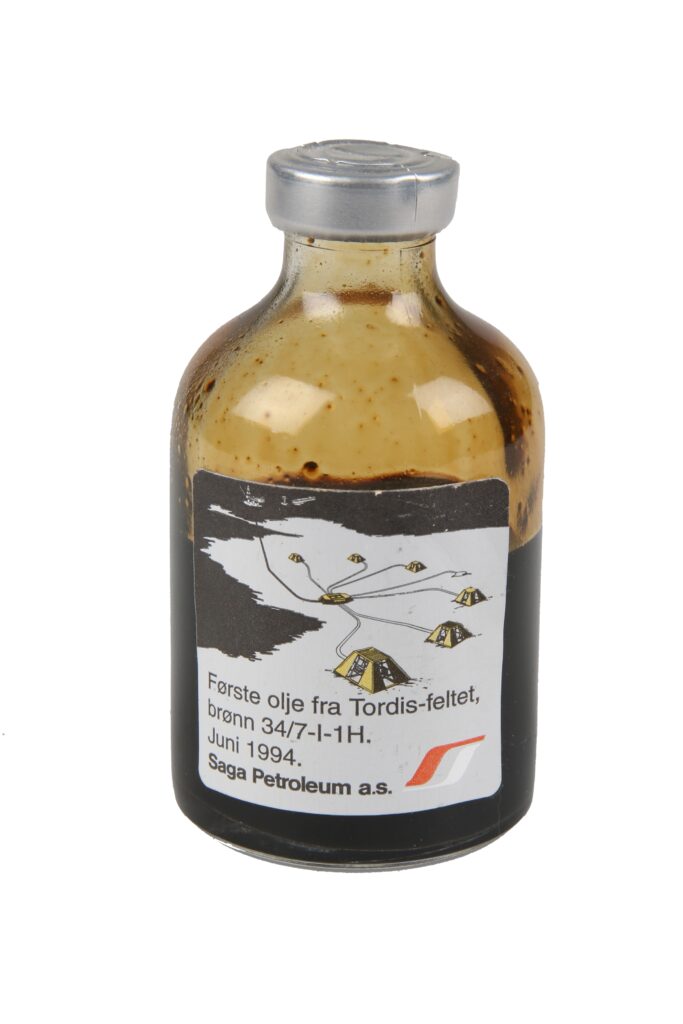
Tordis was originally discovered by Saga Petroleum, and taken over by Statoil when it and Hydro split Saga’s holdings between them in 1999. The field began production on 3 June 1994 as Saga’s second subsea development. It featured a subsea manifold tied back to Gullfaks C and connected to a total of eight satellite wells and two templates. The system included both production and water injection wells.[REMOVE]Fotnote: Gjerde, Kristin Øye and Nergaard, Arnfinn, 2019, Getting down to it. 50 years of subsea success in Norway: 243.
The water cut (proportion) in Tordis output was large, which reduced the amount of oil recovered. Statoil wanted to do something about this, and received approval in 2005 for a supplementary development which involved installing a seabed separation facility. The main principle was that the wellstream should be conducted through the new separator for water removal before the oil returned to the flowline and continued to Gullfaks C. Separated water and sand would be injected via a dedicated well.[REMOVE]Fotnote: Ibid: 244.
FMC Technologies secured the main contract for deliveries to the Tordis subsea separation, boosting and injection (SSBI) facility, as it was now called. The company would collaborate with Norway’s Framo Engineering and Dutch separation specialist CDS Engineering.[REMOVE]Fotnote: Fantoft, R, Hendriks, T and Elde, R, 2006, “Technology Qualification for the Tordis Subsea Separation, Boosting and Injection System”, OTC 17981.
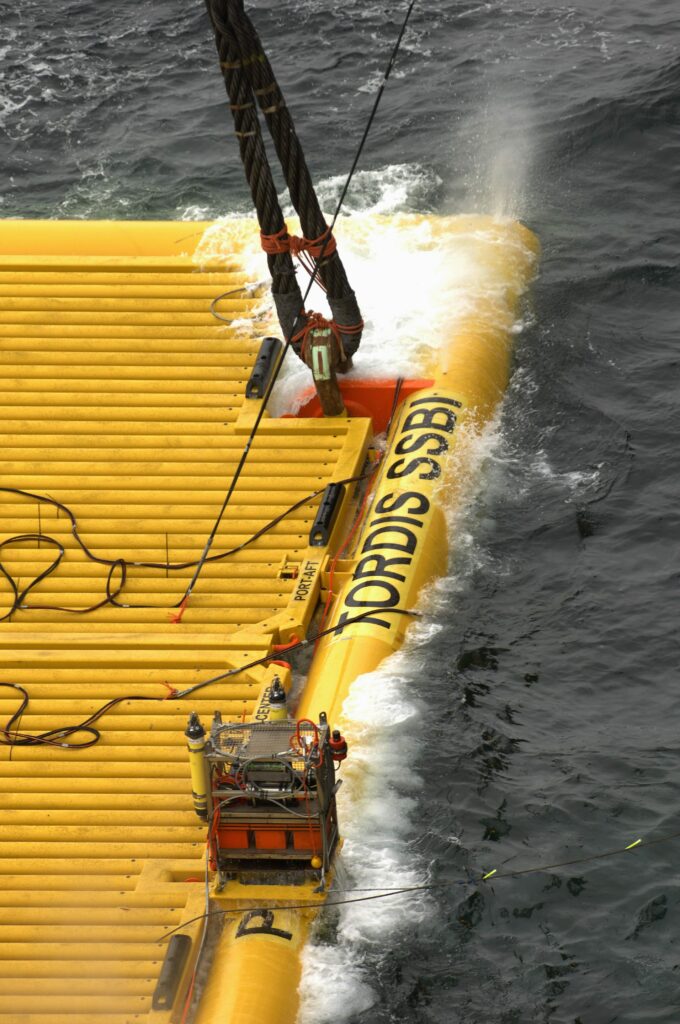
Tordis SSBI was a modular construction, which allowed its main systems to be retrieved to the surface for repair.[REMOVE]Fotnote: Gjerde, Kristin Øye and Nergaard, Arnfinn, op.cit: 245. Thorough testing was required before the facility came on line in October 2007. Following this start-up, the project team found the separator to be effective and that it handled sand as expected. Water injection began as planned, and the system proved to work with high level of uptime. Problems nevertheless arose.
Full shutdown, valuable lessons
An oil slick was reported on the sea surface close to Tordis in early May 2008. Investigations revealed that the oily injection water had found its way back to the surface and created a crater 40 metres long and seven deep in the seabed.[REMOVE]Fotnote: Norwegian Continental Shelf, “Faulty geology halts project”, 16 November 2009. Tordis SSBI was shut down immediately.
After an investigation, the Norwegian Petroleum Directorate (NPD) concluded that Statoil had misinterpreted the geology and that the type of formation which the water was to be pumped into did not exist in this area. The prestige project went into a nosedive. An internal Statoil inquiry found that the incident had caused serious discharges as well as the loss of an injection well, material assets and the improved oil recovery which was to pay for the project. No less than nine key elements in the system had failed.[REMOVE]Fotnote: StatoilHydro, Granskingsrapport – Utslipp av oljeholdig vann og tap av injeksjonsbrønn, 11 August 2008.
Tordis IOR never again operated as intended. It was decided to continue using the separator but to pump the separated water to the platform for treatment and injection.[REMOVE]Fotnote: Ramberg, Rune Mode, Davies, Simon R H, Rognø, Hege and Økland, Ole, 2013, “Steps to the Subsea Factory”, OTC 24307.
This project can nevertheless be characterised as a valuable contribution to technology development on the seabed. It became a basic reference for a number of subsequent initiatives.
A total of 12 subsea separation system were reportedly being planned, in production or shelved globally in 2018.[REMOVE]Fotnote: Offshore Magazine, “2018 Worldwide Survey of Subsea Processing: Separation, Compression and Pumping Systems, Status of Technology as of March 2018”. Of nine cases where the main supplier was named, OneSubsea accounted for two and TechnipFMC for the other seven. The Norwegian initiatives in 1999, 2000 and 2001 have proved to confer world dominance in underwater processing.[REMOVE]Fotnote: Gjerde, Kristin Øye and Nergaard, Arnfinn, op.cit: 246.


