Diving on Statpipe

Pipelaying began in April 1983 with Statoil as operator.[REMOVE]Fotnote: A group of oil companies with interests in the Heimdal, Gullfaks and Statfjord fields formed the I/S Statpipe joint venture, comprising Statoil with 60 per cent, Elf Aquitaine Norge 10 per cent, Norsk Hydro eight per cent, Mobil seven per cent, Esso five per cent, Norske Shell five per cent, Total Marine Norsk five per cent and Saga Petroleum two per cent. See proposition no 102 (1980-81) to the Storting: Ilandføring av gass fra Statfjordfeltet og Heimdalfeltet m.v: 56. Grave doubts attached to this project, and not least the diving aspect. Work dives in such water depths had been the big bottleneck for piping petroleum to Norway from the Ekofisk and Frigg fields.
This obstacle had now been overcome with the development of the saturation diving method, and test dives had been conducted at the Norwegian Underwater Technology Centre in Bergen (Nutec) to verify that descending to 300 metres was acceptable. REMOVE]Fotnote: Gjerde, Kristin Øye and Ryggvik, Helge, 2009, On the edge, under water. Offshore diving in Norway, Wigestrand Forlag: 243–279. How acceptable these verification dives actually were has later been questioned.
Slowly but surely
The pipelay barge started work at Statfjord. It could accommodate 300 lengths of 30-inch pipe on board and received new supplies daily from the coating yard in Åndalsnes, where a protective layer of asphalt was applied.
New lengths of pipe were added to the existing line on the welding deck in the barge, with the welds also covered in asphalt. As the barge advanced slowly but surely by pulling on its anchors, the pipeline descended to the seabed after passing over an aft chute or “stinger”.
Although most of the pipes were welded together on the barge and laid out in their full length, a good deal of welding took place underwater in a dry habitat under high pressure. But the job was planned to avoid such work at the deepest point.
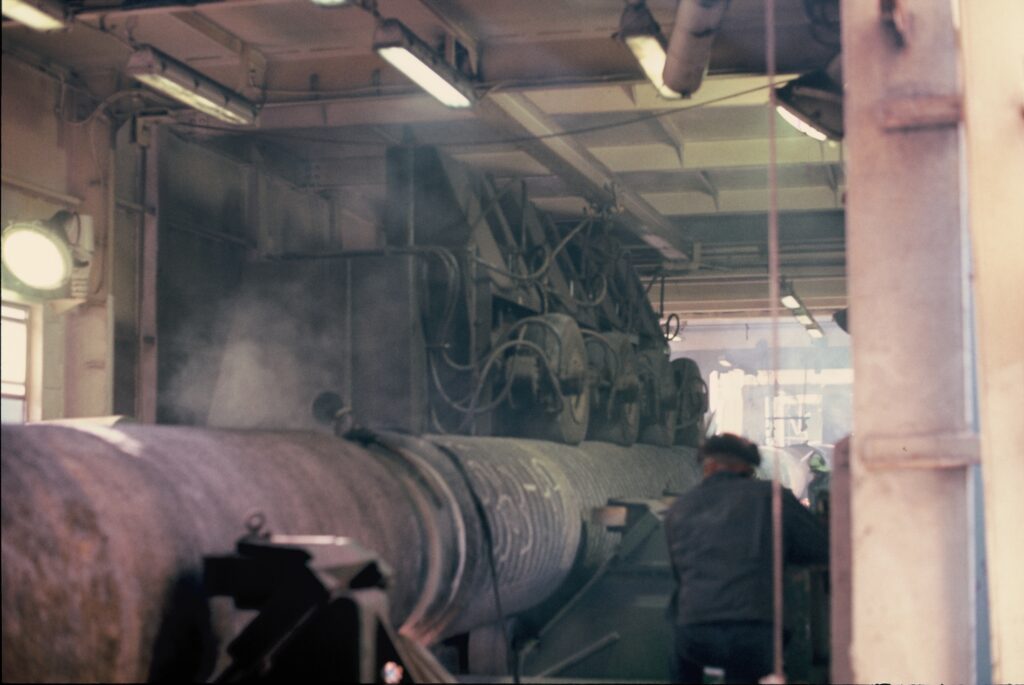
A diving support ship (DSV) always accompanied the laybarge. Since remotely operated vehicles (ROVs) for subsea work were not well developed, divers had to support various operations in water depths varying between 180 and 220 metres.
However, the deepest part of the route ran across the Norwegian Trench, a submarine valley which runs close to Norway’s west coast and is about 300 metres deep. This feature naturally presented first a downward slope and then the upward incline on the other side. The first of these was pitted with a number of “craters”, probably created by natural gas seepage from underlying reservoirs. If crossing one of these depressions created a free span of more than 30 metres, the pipeline had to be given additional support. One way the divers did this involved positioning big bags under a span. These were filled with liquid cement until they became large enough to take the weight of the pipeline. Another option was to use a remotely operated trenching machine to cut ditches which allowed the pipe to lie along the bottom of the crater. Similar problems were encountered on the landward slope, where the glaciers in their time had left deeply scoured strips.
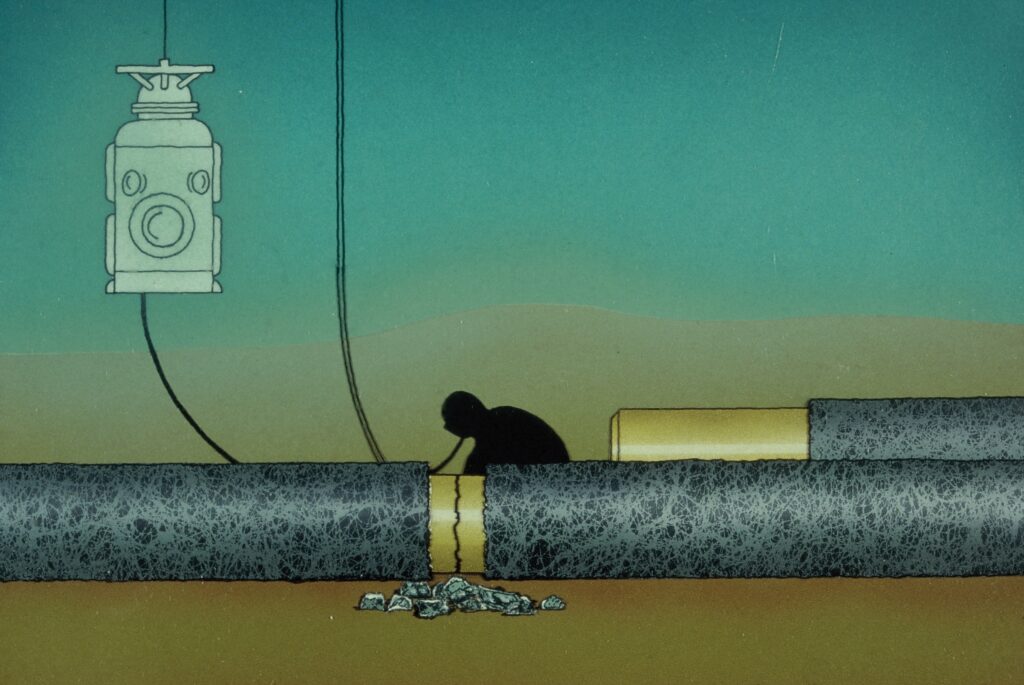
An unusual problem arose when mines from the First World War were suddenly encountered in the middle of the pipeline route. These were blown up to render them harmless. Even after the pipeline had been laid, more mines were discovered further away – but still so close that they represented a hazard. They were removed by using an ROV to net and drag them a suitable distance, so they could be detonated.
Landfall conduit
At the landfall site on the seaward side of Karmøy island, north of Stavanger, divers were needed on a large scale to help Norway’s Selmer construction company build a 600-metre concrete conduit. This was intended to protect the pipeline through the weatherbeaten landfall zone. Waves and tides tore at and wore down the concrete structure from above, below and each side.
The conduit was built in five sections varying from 80 to 140 metres long and towed to the shoreside site,[REMOVE]Fotnote: Statoil, Statpipe bygges, information film, about 1985. where divers were present to assist in positioning them. Since the seabed off Karmøy was uneven, the conduit was laid on six pillars built by the divers – who had a big job to do first in pressure-jetting the seabed. That was followed by drilling into bedrock to secure a secure fixing for the reinforcement bars. Finally, the divers built the formwork for casting the pillars.[REMOVE]Fotnote: Geir Egil Skrunes in conversation with Kristin Øye Gjerde, 25 January 2006. Involving many divers in the 1982-83 period, this work was carried out using surface diving to a maximum depth of 45 metres. The diver market was more or less swept clear.
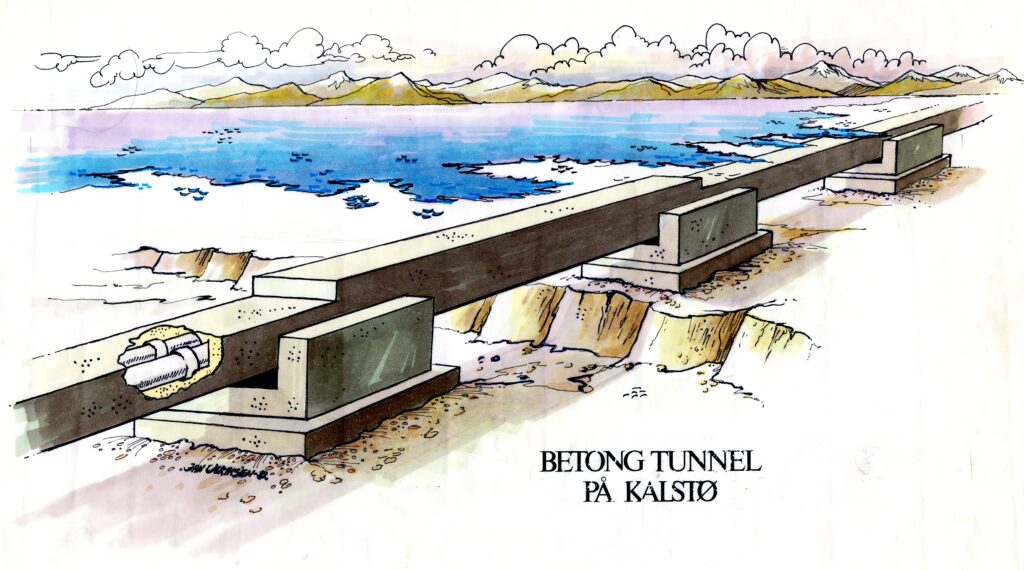
In many cases, offshore divers worked for this project on the side, during their free time on land.[REMOVE]Fotnote: Per Rosengren in conversation with Kristin Øye Gjerde, 13 January 2006. That could be an extra burden on their health, which was already being challenged in their regular job. Investigations showed that divers working on the landfall experienced more cases of the bends (decompression sickness) than normal. The assumed reason was the high waves, which made it harder to achieve the correct ascent speed and/or decompression stops. Working depths also varied considerably during each dive – known as yo-yo diving.[REMOVE]Fotnote: Norwegian Petroleum Directorate, 1994, Rapport om standard dekompresjonstabeller for overflateorientert dykking.
During the final laying phase, the pipeline was pulled through the conduit before being extended across hill and dale to its final destination at Kårstø. The flare was lit there on 25 March 1985 to show that the transport system was in use.
arrow_backStatpipe – an achievementAmericans look to Norwegian gasarrow_forward