Åsgard – a technological quantum leap

This project involved technological innovation on many levels. The choice of seabed wells linked to floating production facilities marked the final step away from fixed concrete platforms. Laying a gas pipeline connecting Åsgard and other fields in the Norwegian Sea via the Kårstø terminal to continental Europe also became financially feasible. But the boldness came at a price. Many technical faults had to be corrected, causing delays and cost increases on such a scale that operator Statoil’s board and CEO had to go.
Unitisation the solution
Åsgard is not a single field, but comprises three discoveries across four licences. Midgard was discovered by Saga Petroleum in 1981, while Statoil found Smørbukk and Smørbukk South in 1984 and 1985. The two companies long considered separate developments, but no progress was made because these finds were individually non-commercial. Water depths of 240-300 metres made any project demanding.[REMOVE]Fotnote: This article builds on chapter 10 in Getting down to it. Fifty years of Norwegian subsea success, by Kristin Øye Gjerde and Arnfinn Nergaard, 2019.
An opportunity to get started arose in 1994. New gas sales to the continent were on the cards, and developing the Halten Bank fields as a unified whole could make available the resources Europe required. This was complicated because nine licensees and two operators were involved across the four licences.
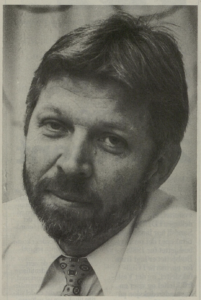
To achieve a development, the oil companies had to look beyond their own narrow interests. Kyrre Nese, responsible for field development at Statoil, contacted Lars Bjerke, Saga’s vice president for exploration and production, and presented a proposal to unitise the three fields with his company as operator and Bjerke’s with a development role. As compensation, Statoil would transfer the operatorship for the Fenris discovery (later renamed Varg) to Saga.[REMOVE]Fotnote: Kyrre Nese interviewed by Kristin Øye Gjerde and Arnfinn Nergaard, 21 February 2018. The two companies thereby reached agreement.
That marked the start to demanding negotiations between the nine licensees on unitised development and operation of the Åsgard area, with Statoil as operator. Various farm-ins and farm-outs reduced the number of licensees in the unitised licence to seven. Statoil was the largest at 61 per cent, with Saga, EssoMobil, Neste, Eni, Total and Norsk Hydro sharing the remainder.
At the end of 1994, Statoil established a joint team for project planning and development where Saga personnel held key roles. Nese was put in charge of the whole project, which included drilling and completing wells in addition to readying for production.
Nail in the coffin for concrete
The concept of subsea wells tied back to production floaters was not the obvious choice for Åsgard at first. Five possible development options were considered in the impact assessment.[REMOVE]Fotnote: Statoil/Saga, Åsgard konsekvensutredning, December 1995. The field covered an extensive area and required several installations in any event.
Initially, at least one of these was planned as a fixed concrete gravity base structure (GBS) standing in 244 metres of water – probably with a single support shaft, like Draugen.
Norwegian Contractors (NC), which had a monopoly for building such structures, was fairly confident of winning the assignment. While the various options were being assessed, however, the concept of replacing the fixed platform with a production ship was matured. Statoil gradually acquired greater confidence in a solution of this kind. However, the Norwegian Petroleum Directorate (NPD) remained unconvinced – and strongly recommended the choice of a concrete installation with drilling facilities.
Several factors had to be assessed when selecting a concept. Price was one. The impact assessment estimated that a concrete platform would cost NOK 10.3 billion, while a floater was cheaper at NOK 7 billion.
However, price was not the only consideration favouring a floater solution. Since the field was extensive, measuring 60 kilometres from north to south and 20 from east to west, it would be difficult to drill enough extended-reach wells from a single concrete platform given deviated drilling methods at the time. Tying back a large number of subsea wells to a floater provided much greater flexibility and more opportunities to increase the recovery factor on the field.[REMOVE]Fotnote: Kyrre Nese interviewed by Kristin Øye Gjerde and Arnfinn Nergaard, 21 February 2018.
When the plan for development and operation (PDO) for the field was delivered in December 1995, the concrete solution had been dropped. That was dramatic for NC, and meant the nail in the coffin for both concrete platforms and the company. It was a big employer, and the end of GBS construction meant some adjustment in the Stavanger area. Troll A, completed in 1995, was the last such structure to built in the city’s Hinnavågen district.
Åsgard solution
The PDO for Åsgard was approved on 14 June 1996, with a production ship for oil processing and intermediate storage and a floating gas treatment platform to process and export gas. In addition came a monohull unit for intermediate storage of condensate.
Nese was the driving force in getting Statoil to dare take this technological leap. This message was more or less hammered home against opponents in the organisation who would have preferred to rely on known technology.
Åsgard was a large and demanding project. While the kick-off meeting assembled 17 people, the number working to realise it peaked at 10 000. It was organised in four units, each with its own director – one for each floater and the fourth for the subsea installations.[REMOVE]Fotnote: Helge Hatlestad was given overall responsibility for the Åsgard development, with Saga’s Torstein Vinterstø as project director for the subsea facilities.
The most spectacular aspect of the development was the number of flowlines, cables and umbilicals on the seabed. Seventeen “yellow box” templates with four well slots in each were not only tied back to their respective parent installations but also linked together for common functions.
Project planning took place at a time when the aim was for as many of the technical solutions as possible to be standardised. Development of the Norwegian continental shelf (Norsok) standards progressed at full tilt in the mid-1990s. These were expected to both cut project costs and reduce the time taken by 30-40 per cent. The yellow templates chosen conformed to a standard of this kind. They had a fold-up design and were installed over three summers in 1997-99.
A number of systems were developed as work progressed, each of them representing substantial innovations. Underwater multiphase flow meters provided operating personnel with continuous information on the various liquid/gas mixes in each well so that production could optimised. Flowlines were improved by installing insulation which coped with high temperatures. In addition, direct electric heating of flowlines was adopted. And enhanced remotely operated tools for connecting flowlines to Xmas trees were developed.
Installations on Åsgard
Handling oil output from the field, Åsgard A ranked at the time as the world’s largest and most advanced production ship. That status also applied to the swivel at the base of the hull. This was the critical component for transferring all the lines linking ship and subsea installations while still permitting the vessel to weathervane freely.
Åsgard C was a storage ship used to hold the condensate produced not only from the field but also eventually from other developments.
Gas from three different formations with differing properties and blends was received and processed on Åsgard B. This treatment yields rich gas, oil, condensate and injection gas in four product streams.
Transferring gas from a moving platform to the seabed for export was complicated. The solution was to use flexible high-pressure risers. Since such pipes were not available in the same large dimensions as the 42-inch seabed pipeline, two-three parallel export risers with smaller diameters were used. These were installed with a “lazy S” curve before reaching an export riser manifold on the seabed which transferred the gas flow to the pipeline.[REMOVE]Fotnote: Offshore Magazine, 1 April 2000.
The technology was new, and problems arose. These included powerful vibrations and noise from the export risers experienced on Åsgard B from the start. The vibrations propagated throughout the platform and felt very uncomfortable.[REMOVE]Fotnote: Henrik Carlsen interviewed by Kristin Øye Gjerde and Arnfinn Nergaard, 27 January 2017 Efforts were made to mitigate the problem by reducing production, but this was not enough. After a while, fatigue fracturing and gas leaks occurred in two small branch pipes. Installing new risers overcame the problem, but it took time before the planned total production capacity was reached.
A man from Shell once took me aside and said that his company would never have managed to implement Åsgard. The traditional attitude was that you should know everything before starting. We said that we know some of it, but have faith.
Looking back, we were undoubtedly unaware of how risky this development was. But there was great determination to accomplish it. I would never want to have missed the time on Åsgard, we felt that we were involved in doing something big. Kyrre Nese, project head.[REMOVE]Fotnote: Kyrre Nese interviewed by Kristin Øye Gjerde and Arnfinn Nergaard, 21 February 2018.
The gas flows from Åsgard B to Kårstø north of Stavanger through the Åsgard Transport system. With a diameter of 42 inches (107 cm), this pipeline runs for 707 kilometres. From Kårstø, the gas continues to continental Europe. The ÅTS carries gas not only from Åsgard, but also from other fields on the Halten Bank. That made gas deliveries to Europe more stable, since exports by one field could be replaced with supplies from another if problems arose.
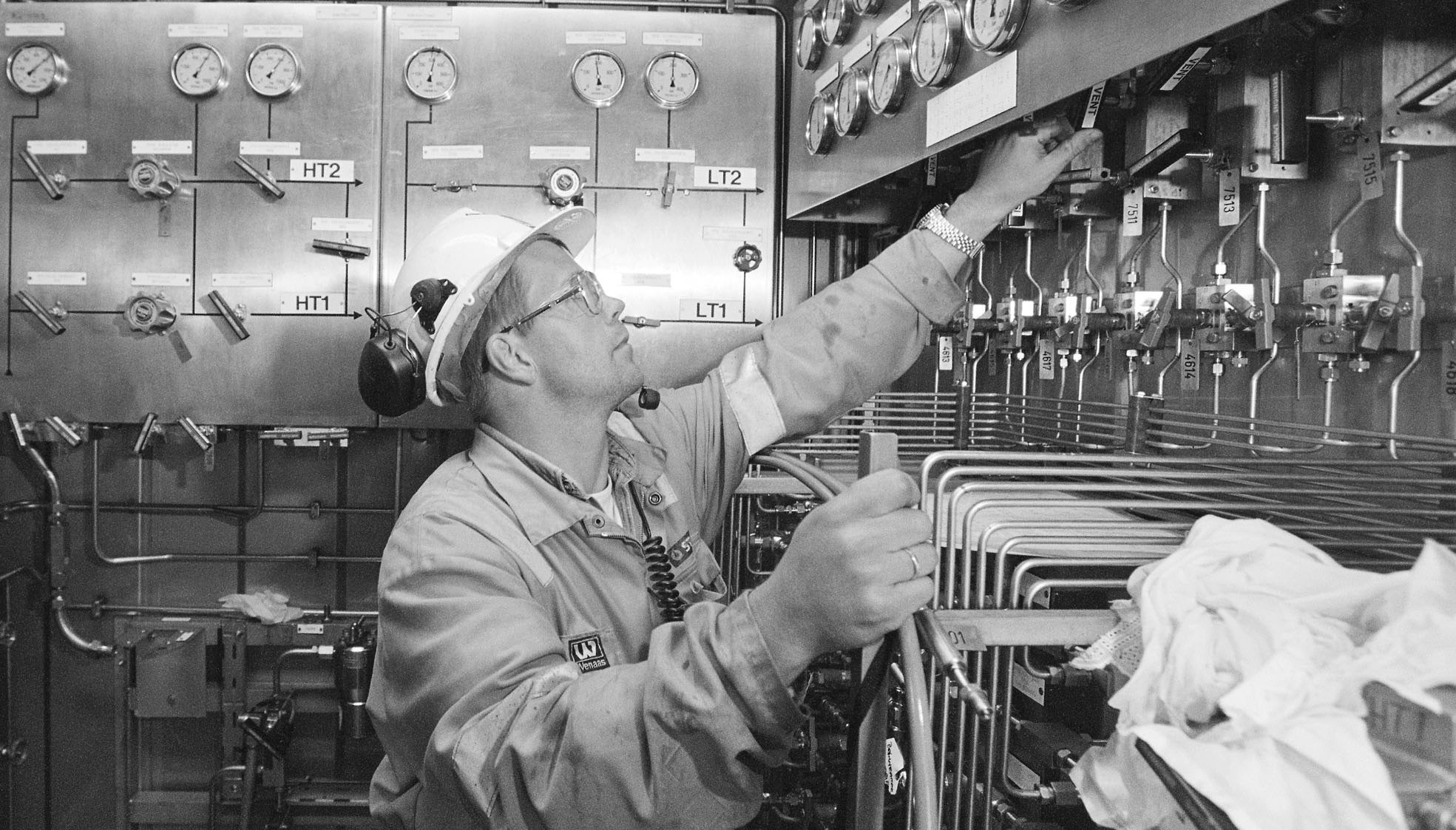
Overruns…
When the start to production on Åsgard A was celebrated in May 1999, not everybody who had been involved in the process was able to attend. Nese, the long-serving project leader, had left on 1 January.[REMOVE]Fotnote: Nese became head of field development at Statoil in July 1990, and thereby became responsible for the Halten Bank. When he left Åsgard, he had held that responsibility for 8.5 years. He then served as operations vice president on Sleipner for five years. The Åsgard development had massively exceeded its budget. Published in February 1999, the Kaasen report analysing investment developments on the Norwegian continental shelf revealed a cost overrun of NOK 8.4 billion, or 30 per cent, at the time of writing.[REMOVE]Fotnote: Norwegian Official Reports (NOU) 1999:11 Analyse av kostnadsutviklingen på sokkelen (Kaasen report), https://www.regjeringen.no/contentassets/5375e71e9c514023b13b24e6437a9b7f/no/pdfa/nou199919990011000dddpdfa.pdf.
That was not all. The project also covered the Åsgard Transport pipeline to Kårstø, the expansion of facilities at the latter, and the Europipe II gas pipeline from Kårstø to Emden in Germany. Investment totalled NOK 64 billion in April 1999.[REMOVE]Fotnote: This broke down into NOK 39.1 billion for the field, NOK 8.1 billion for the pipeline to Kårstø, NOK 9.6 billion for the Kårstø receiving facilities, and NOK 7.2 billion for Europipe II.
A project supposed to cost NOK 48 billion was set to end up at NOK 66 billion – an overrun of NOK 17 billion. Acting petroleum and energy minister Anne Enger Lahnstein from the Centre Party was not happy with that. On 23 April 1999, she dismissed the whole Statoil board. CEO Harald Norvik resigned.[REMOVE]Fotnote: https://www.vg.no/nyheter/innenriks/i/wEeee5/styret-i-statoil-maa-gaa-av, accessed 23 April 1999.
… and leaks
But the problems were not over. In early 2001, gas bubbles were observed from the subsea installations. An inspection revealed crack formation in a weld. For safety’s sake, all welds of the same type – no less than 72 – had to be checked.[REMOVE]Fotnote: Annual report, 2000, Statoil, February 2021. Åsgard B had to be shut down while Statoil mapped the extent of the problem. No less than 24 welded joints in the flowlines out to the various production wells around the platform had to be repaired, while the rest were given a clean bill of health.
A further leak was reported from the seabed facilities in August that year, now involving one of the supposedly “healthy” welds. Åsgard B had to shut down again.[REMOVE]Fotnote: VG, 13 August 2001.
The fault was that end pieces began to crack after production had been under way for a time. In some cases, the cracking was so serious that the components fell off.[REMOVE]Fotnote: Asle Solheim interviewed by Kristin Øye Gjerde and Arnfinn Nergaard, 20 January 2017. Metallurgists and corrosion specialists had big problems understanding what was happening. They finally concluded that the welds were not covered by the protection of the sacrificial anodes, leaving them exposed to corrosion. That led to hydrogen embrittlement in the material and consequent cracking.
Statoil decided that all 72 welds had to be repaired at a cost of no less than NOK 2.6 billion. In addition came billions in deferred revenues from suspending gas production.[REMOVE]Fotnote: Norwegian Broadcasting Corporation (NRK), 30 October 2001, https://www.nrk.no/trondelag/asgard-b—et-milliardsluk-1.120761. ABB, which had been responsible for the delivery, found itself in trouble. Fortunately for the company, it reached an amicable settlement with Statoil, since no clear conclusion could be reached about where responsibility lay.
Although Åsgard had a difficult start, the continuation has been brighter. In 2020, the field embraced 70 wells and 23 templates. A gas compression facility installed on the seabed in 2015 was the size of a football pitch and represented completely new technology which helped to boost production. Over two decades, Åsgard has produced oil and gas with an estimated value of just under NOK 1 000 billion. That is something Norvik, who had to resign over the budget overruns, can probably feel very satisfied with.
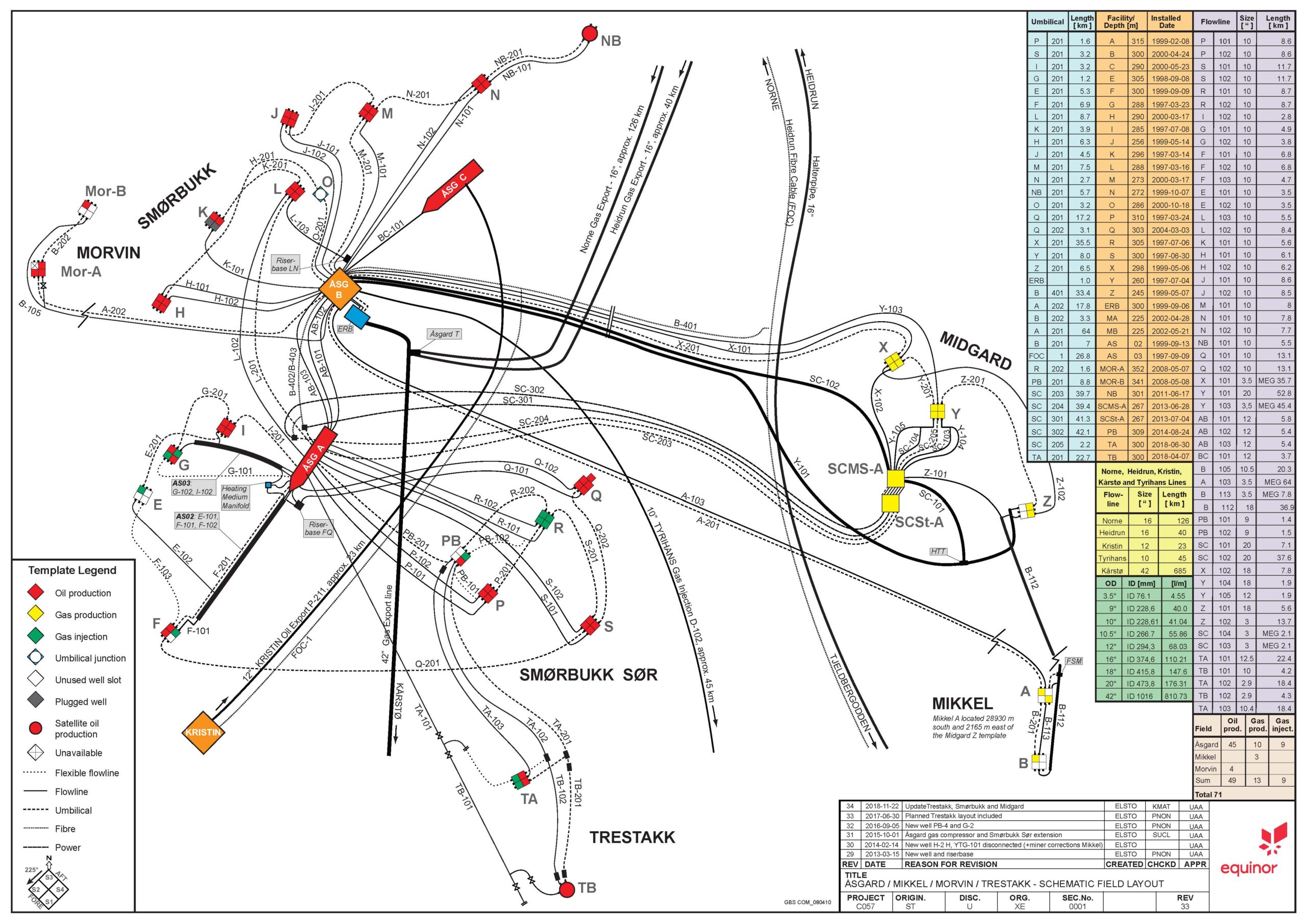